Author: French fries fish
“The forever unattainable is always stirring”…
What Eason Chan sang in “Red Rose” wasn’t just about love.
Using “once again, twice again” to describe the twists and turns between me, an automotive editor, and the common Altium platform is quite appropriate. In March of 22 in Shanghai and November of 22 in Beijing, I missed the offline activities of Altium twice because of the pandemic.
Fortunately, Buick made up for the “never again”.
As Buick’s first electric car based on the Altium platform, the Buick Electra E5 was born in the Altium Super Factory in Wuhan. And I was able to witness the true face of Altium in its home.
Safety when opening the cover
In the past, I thought the most eye-catching point of Altium walking around the world was intelligence. After all, wBMS wireless battery management technology “I have it when others don’t”, and new solutions that can save 90% of the harness of the battery pack can always evoke everyone’s “wireless” imagination.
Now, when Buick really dismantles the Altium battery pack step by step into battery cells according to the division on the PPT, and presents them one by one in front of you, this is much more convincing than a PPT with 10,000 pages. As for Buick’s core to convince us, it is safety.
Buick said that to do a good job of battery pack safety, they summarized three points: heat insulation, exhaust, and arc prevention.
But you might not imagine that when it comes to the heat insulation safety of Altium battery packs, the first thing Buick showed us after opening the top cover of the battery pack was actually several “straw mats”. The term “straw mat” originated from the jokes made by other media present about its appearance. They are actually fireproof blankets built into the battery pack and the last insulation wall between the battery pack and the passenger compartment.
It consists of various components including high silicon-oxygen cloth and aerogel. Aerogel is responsible for thermal insulation, but it suffers from low structural strength. In the event of a short circuit inside the battery pack, high-temperature and high-pressure gas could instantly destroy the aerogel structure. That’s when the high silicon-oxygen cloth comes into play. This material is not a thermal insulator but is strong enough to hold the aerogel firmly together, thereby forming a high-strength insulation and fireproof blanket.
Under the blanket is the energy body of the battery pack. Buick demonstrated the battery cells and different disassembled states of the battery modules of Oltenergy.
The elongated dark blue strip at the bottom left of the above figure is the battery cell. The light blue elliptical ring on the top of the cell is a safety valve. When an accident occurs, high-temperature and high-pressure gas will be discharged from the valve. Our focus should then shift to the module level. In order to ensure insulation and thermal insulation, Oltenergy set a mica sheet on the upper part of the cell. Pay attention to these mica sheets, their thickness is not uniform. At the corresponding position of the cell safety valve, the mica sheet will be thinner to facilitate the further outward diffusion of the high-pressure hot gas.
At this point, the gas has already rushed out of the module and reached the battery pack level. Oltenergy set a centralized exhaust channel at the axis line of the battery pack. The ultimate outlet of the exhaust channel is the safety valve of the battery pack, which can completely release the high-temperature gas from the battery pack and avoid heat diffusion.
There is also arc prevention. When a cell fails, the high-pressure hot gas that is discharged may also carry some conductive powder from inside the cell. When these conductive substances fall onto the high-voltage components of the module, it is easy to cause a short-circuit arc, which can be simply understood as an electric spark. Oter Energy covered the high-voltage component area of the module with a layer of high-temperature resistant insulation material, which is the silver-gray substance on the two sides of the cover of the module, in order to prevent short-circuiting and avoid arcing.
As for the conspicuous circuit board on the module, it is an important component of the wBMS, used to collect and detect module information and report it. In terms of safety, Oter Energy can monitor in real time at the highest detection frequency of 10 times per second. In terms of efficiency, the streamlined 90% harness not only reduces assembly difficulty, but also provides higher flexibility for Oter Energy’s platform to cover various vehicle models.
And flexibility is the biggest impression I have felt in Oter Energy’s production workshop.
Flexibility is King
As Oter Energy’s platform needs to cover many vehicle models from cars, SUVs to MPVs, from entry-level to luxury models, Oter Energy is very flexible, or to use a more professional term, “highly flexible,” since the beginning of production.
To achieve this goal, General Motors has applied “robotics, 3D point cloud vision and force control perception” fusion technology in many workstations in the Oter Energy production workshop.
At the battery module assembly line station, we saw a disassembly of a 10-module battery pack nearby, but at this time, the production line had already switched to an 8-module battery pack. The robot arm can automatically recognize and grab the battery module on the material tray, and then transfer it to the battery pack shell. When there are no modules in the tray, the robot can also automatically stack the tray to obtain new modules. With the help of 3D point cloud vision technology, not only can the types of battery packs produced be more flexible, but also the installation accuracy of the modules has reached 0.2mm.The Chinese Markdown text with HTML tags preserved:
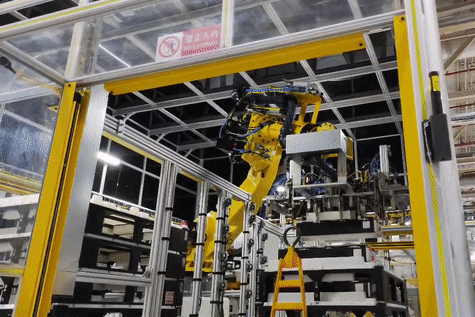
随后,固定模组的 6 颗螺丝能同时被一次性拧紧。在这过程中,拧紧螺丝的扭矩、角度都将被一一记录,实现质量可追溯。
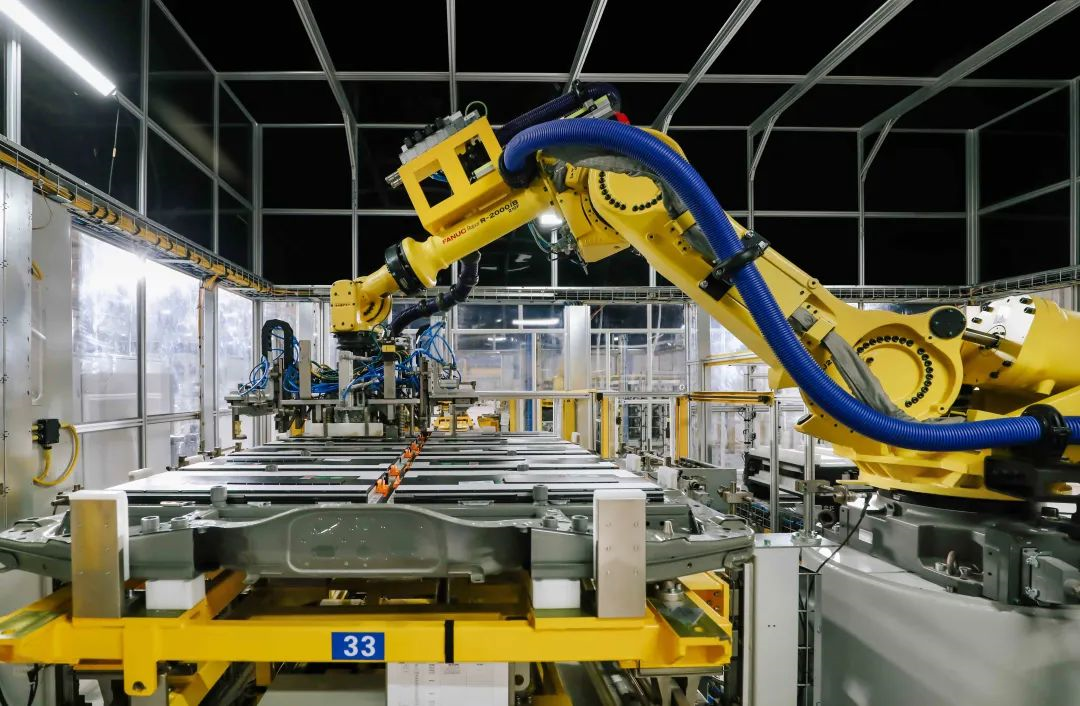
柔性概念在电池包上盖的涂胶工位也有表现。与常见的机器人涂胶工艺不一样的是,奥特能电池包上盖的涂胶,通用采取了「**涂胶头固定不动,上盖转动**」的方案。
乍一看,这太不合理了。为什么要固定体积更小的涂胶头,而去挥动一大坨电池包上盖?对此,别克工程师给出的解释是,这样的空间利用率更高 —— 涂胶头虽小,但如果要让涂胶头跑完整个上盖的边缘轮廓,就必须为涂胶头设置一个比上盖投影面积更大的移动装置;相比之下,转动上盖看似是大动作,但机械臂其实只需进行更小幅度的摇摆和转动即可完成涂胶工作。即便是切换到更大模组的电池包生产上,也依旧游刃有余。
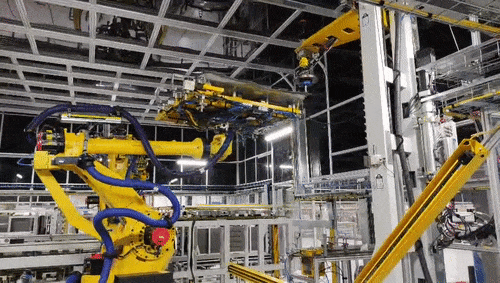
像上面动画里展示的涂胶动作,同时还包含了数字孪生的技术。涂胶方案在设计时会经过数百次模拟仿真和调优,执行涂胶动作时,一旁的工控屏会以绿色线条实时显示机器人的涂胶位置,最终能实现 0.1mm 的安装精度。
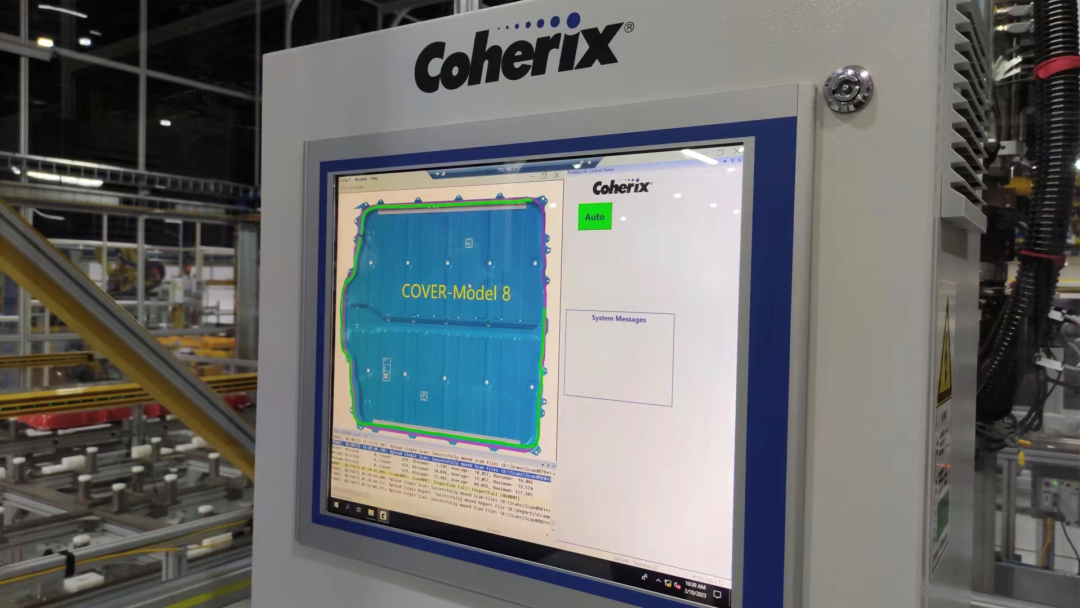
像这样的智能化自动化生产,不仅是在电池车间,还有电驱车间。
Introduction
The Wuhan Auton Super Factory’s EV drive workshop utilizes manual visual detection and hoisting during feeding. From processing to cleaning, testing, inspection, and offline, it’s all performed automatically. Currently, Auton’s motor stator and rotor assembly achieve an accuracy of 50 microns, which equates to the thickness of a human hair.
Both internal strength and external performance are required
Although there are many focal points to be remembered, a half-day tour is clearly insufficient for such a large factory.
From the manufacturing perspective, I can perceive the concepts that Auton’s platform has established from the outset, such as flexibility, efficiency, and continuous implementation throughout the manufacturing process. Nonetheless, it is clear that I desire to learn more about the extent to which Auton is flexible, efficient, and to what degree?
Because a few competitors have proven the huge cost advantages brought by flexibility and efficiency, feedback to the terminal selling price of automobiles can become a strategy of price attack. Specifically, in 2023, electric vehicle competition will become more brutal.
Even though technology is fantastic, it still needs products to speak for it. Even though the platform is excellent, it still needs to be measured by vehicle models.
Fortunately, Buick’s first Auton platform pure electric SUV Electra E5 has already been rolled off the production line from the Wuhan factory.
It is time to accelerate; is this the new era of Buick’s electrification?
This article is a translation by ChatGPT of a Chinese report from 42HOW. If you have any questions about it, please email bd@42how.com.