Writing | Roomy
Editor | Zhou Changxian
The debate over whether CTP (Cell to Pack) battery pack technology or CTB (Cell to Body) technology is better has always been ongoing, without a “standard answer”. This is similar to the debate over whether autonomous driving is a pure visual solution or a LiDAR solution.
This is a good thing. Diversification of technological development and the different opinions represent a thriving industry. By the time this article was written, BYD, which cannot be ignored in the field of electric vehicles and battery technology, had a market value of over 1 trillion and a P/E ratio of over 300.
According to rumors in the industry, Wang Chuanfu, also known as “Old Wang”, is good at gambling and has even gambled out a trillion-dollar market value. Currently, BYD’s total market value is 1.02 trillion, just one step away from Ningde Times with a market value of 1.06 trillion. It seems that surpassing Ningde Times is just a matter of time. Many people are worried that Wang Chuanfu will lose his title as “King of Batteries”.
Looking at Wang Chuanfu’s cards, they are clear and immense. The full industry chain layout and the insistence on lithium iron phosphate batteries and production of blade batteries are the two cornerstones supporting Wang Chuanfu’s “bold gamble”.
BYD is the only automaker in the world that has full core technology for new energy vehicles, including batteries, motors, electric control, and chips. Recently, BYD released the CTB battery-body integration technology and the first model equipped with this technology – BYD Hippo.
As a result, the debate over which battery pack technology is superior, CTB or CTP, has arisen again, implying “who is the battery king”? After all, Ningde Times will also release the CTP3.0 Kirin battery, with higher energy density and range than the Tesla 4680 battery…
The Kirin battery and the CTB battery are the highest technologies held by Zeng Yuqun and Wang Chuanfu, respectively, and are considered the critical points of technology competition. In a moment, the battle was fully under way.
In addition to BYD and Ningde Times, there are many forces eager to join the fight. In April, Leap Motor released a new power battery packaging technology, CTC (Cell to Chassis) technology. In June, SAIC also revealed the “Magic Cube Battery”, with lying battery cells as its killer feature…
All parties have significant chips, hoping to establish their foothold in the vast world of electric vehicles.
CTP Battery Technology Welcomes Structural Innovation Again
Do you still remember the opinion expressed by a chip company in a previous interview, “Once an automaker selects a chip or battery, it is unlikely to change because of issues related to vehicle safety performance and compatibility. Even if someone else introduces something that is technologically superior, it may not be selected.”
Therefore, seizing market share has become a key factor in expanding the technological route. That’s right, it needs teams, as well as endorsements.According to the technical stage, SAIC’s “Magic Cube” battery, Great Wall Motors’ “Dayu Battery”, and Guangzhou Automobile Group’s “Magazine Battery” all mainly adopt CTP technology, and can be regarded as advocates of the CTP technology route.
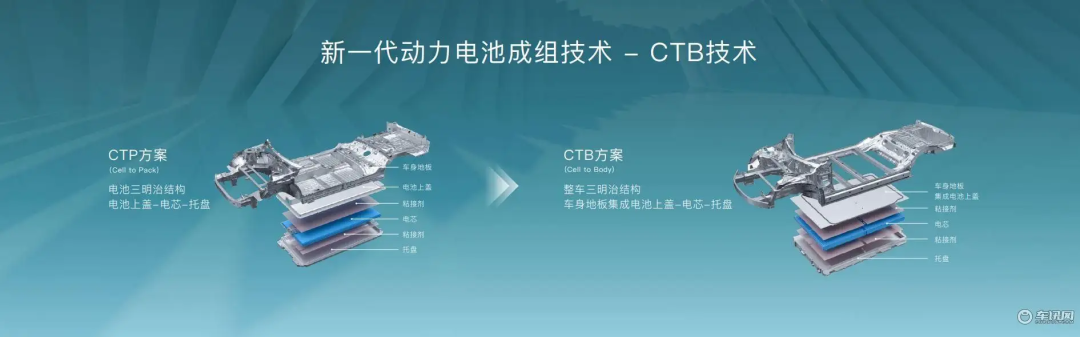
BYD’s CTB (Cell-To-Body) technology for battery integration is an upgrade based on CTP technology, and eventually evolved into battery-body integration technology, referred to as “the ceiling limit of fuel vehicles becoming the lower limit of electric vehicles.”
Since 2019, Ningde Times has released a first-generation CTP battery technology structure suitable for passenger vehicles, which has changed the old pattern of electric vehicles, and the “battery technology competition” has become a new topic of competition.
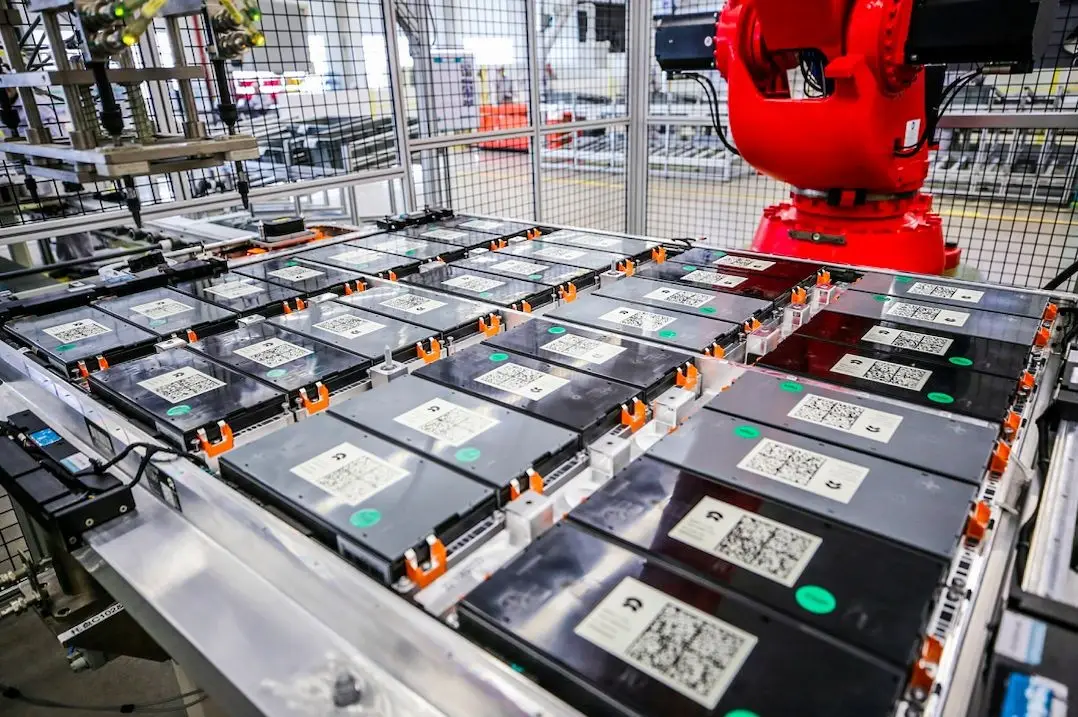
To explain the term, a battery pack, also known as Pack, is composed of a battery management system (BMS), electrical system, structural components, thermal management system, and modules. Among the modules, the core energy storage unit of the battery, the battery cell, is arranged and distributed.
In layman’s terms, CTP technology directly integrates the battery cells into the battery pack by removing the module design. The battery pack is also integrated into the vehicle body as a structural component on the vehicle floor. The advantage is that the space utilization and volume ratio of the battery are greatly improved, making the battery layout no longer in a “fat boy” state.
Currently, there are three common battery technology schemes: CTP, CTB, and CTC. It is necessary to first complete the CTP technology to achieve CTC and CTB. BYD’s “Blade Battery” also belongs to CTP technology.
There are two routes of current CTP technology: the module removal plan, such as BYD’s “Blade Battery”. The integration of small modules into large modules, represented by Ningde Times.
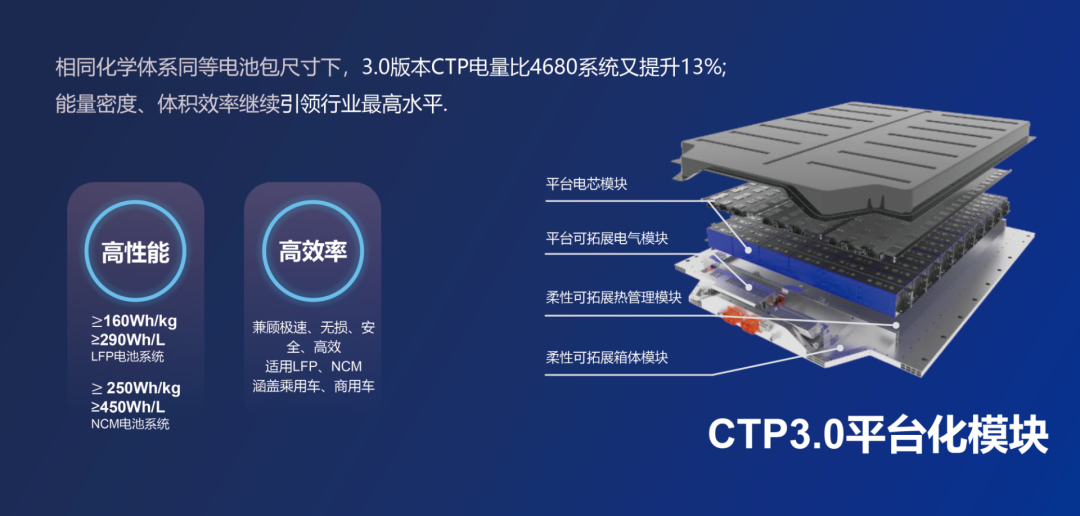
Before the pride of Ningde Times, the third-generation CTP technology is put into mass production, the CTP battery route has a new action, which is known to have added chips to the competition between Ningde Times and BYD. This is the recently released SAIC Magic Cube battery, known as the “ultra-thin and flat” battery, which means that the CTP battery structure has further innovation.Vice President of SAIC Data Business Department, Chief Digital Officer of Passenger Car Company, and CEO of MG Brand, Zhang Liang, said that the “Magic Cube” battery is essentially CTP grouping technology, and the horizontal battery design is one of the important advantages, which can reduce the thickness of the CTP battery pack to as low as 110mm. The space of the whole vehicle is increased and the energy density of the battery is increased to 180Wh/kg, greatly improving efficiency.
“Our first idea was to create a battery platform that would meet the needs of all car models. The first requirement was that the battery pack must be small and thin enough. If we use the original layout method, the battery pack is less charged and not suitable for medium to large vehicles that require more than 80% electric power.”
At present, almost all the electric vehicle battery components on the market use a vertical cell layout inside. However, “vertical cell layout has a limit”. Zhu Jun, Deputy Chief Engineer of SAIC Group and General Manager of Jetson, believes that the greatest advantage of the horizontal cell layout is its high integration and greatly improved space utilization of the battery pack.
According to Zhu Jun, CATL had explored the horizontal cell layout before, but due to the challenges in structure and cooling, it remained at the conceptual stage. This time, SAIC and CATL have worked together for more than two years to solve this problem.
He used a metaphor to explain the advantages of the horizontal cell layout structure. “Just like a deck of cards, the original cell layout of the battery pack was vertical, but now it is laid down horizontally. Not only is the thickness smaller and the weight lighter, but the space used and the contact surface are also very small, which brings about an improvement in space efficiency and zero thermal loss.”
For different battery capacities, “Magic Cube” batteries provide three different battery module thicknesses: 110mm, 137mm, and 125mm. The larger the battery thickness, the more cells it can accommodate. However, the structure of the Magic Cube battery is that the length and width remain the same as the thickness increases. According to SAIC, the longest battery pack is 64kWh, which can last up to 12 years or 1 million kilometers. The outstanding feature of the Magic Cube battery is its long life.
Alternatively, it can be said that the launch of the Magic Cube battery has added many possibilities to the CTP technology led by CATL, the CTB technology of BYD, and the CTC battery technology of Leapmotor.
“I don’t think CTB/CTC or CTP is perfect in every way, they all have their own advantages and disadvantages.” Zhu Jun believes that even though the routes are different, everyone has the same goal of promoting the development of electric vehicles.
Who is the future?No matter whether it’s BYD’s CTB or Linglong’s CTC, they share a distinctive feature – high integration and modularization, which shows the mastery of the chassis hardness and structural design by the automakers.
Previously, CTP technology was unable to break through the pack and still relied on the “battery pack”. In other words, the battery is the battery, the chassis is the chassis, and carmakers and battery companies could be independent of each other. This has caused a headache for carmakers where “power battery manufacturers have great say, even control the lifeline”. Therefore, the saying “the world is suffering a long time” is commonly circulated in the industry.
The competition for control led naturally to the automakers’ desire to master battery technology. GAC’s MagShot battery adopted a shell safety design, and each individual cell in the battery pack is placed independently inside the safety shell; Great Wall’s Da Yu battery is more like a battery platform that can accommodate different positive electrode material ratios… All these indicate the urgency for carmakers to gain dominance.
BYD’s Dolphin’s CTB platform and Linglong’s CTC technology have similar objectives in pursuing a fully integrated chassis, which is also the most direct way to take control. BYD’s CTB technology integrates the battery pack upper cover with the traditional structure of the vehicle chassis, while Linglong’s CTC technology breaks through the limitation of the “battery pack” and integrates the battery into the body structure.
Of course, CTB and CTC have their differences.
BYD’s CTB technology utilizes the high structural strength of blade batteries to place the battery pack as a separate component on the entire vehicle floor. The battery pack’s upper cover is connected to the vehicle body bottom, which creates a structure similar to a battery-body integrated design. Strictly speaking, it is different from the CTC battery-body integrated design.
In terms of integration, the CTB technology is slightly inferior to the CTC technology scheme, owing to the difference in whether the chassis is fully stressed. Actually, BYD’s CTB technology has a sense of “above CTP, but not yet CTC”. Industry insiders believe that BYD’s CTB technology and SAIC Magic Cube battery can be considered different innovations in CTP battery technology structure. The CTC technology is a complete model of battery-body integration.
CTC technology cancels the pack design and directly installs the battery core in the one-piece stamping formed plate, thereby making the chassis and battery into one. The advantage of doing so is, for example, that in the case of Linglong’s CTC technology, it can increase the vertical space of the entire car by 10mm and increase the battery layout space by 14.5%…
Actually, it’s not LI that adopted CTC technology first, but Tesla, as the first car manufacturer in the world to mass-produce CTC technology. Currently, Volkswagen and Volvo have also announced their plans to develop CTC battery technology in the future, and CATL is also planning to officially launch highly integrated CTC battery technology in 2025. This fully demonstrates that integrated battery and car bodies is the trend. Guohai Securities analysis also believes that by 2030, CTC battery technology is expected to reach a penetration rate of 60% in the new market for electric vehicles. However, whether it’s electric vehicle products or power battery technology, safety performance is the most core focus. Compared with mature CTP technology, CTC technology is relatively new, with fewer production models and requiring more data support for safety verification.
“Some car manufacturers combine the bottom plate with the top cover of the battery, which reduces the weight and space of the bottom plate, but the problem is that once the side of the car is collided, it is easy to deform the bottom plate and the associated upper cover, which causes the sealing to disappear.” Although Zhu Jun said that there is no difference between CTP and CTB/CTC in terms of advancement, the risk of collision may cause the entire battery pack to be replaced, and “the maintenance cost of CTB/CTC is still higher.”
Therefore, the mature evolution of CTC technology requires time, leaving a certain development space for structural optimization of CTP technology.
The SAIC new MG MULAN model is equipped with the SAIC Mofei battery, which answers the question of what “development space” is. The Mofei battery, based on CTP technology, has a unique advantage in that it supports both charging and battery swapping. Although CTB and CTC technologies are more integrated in terms of structural design, they can only be charged because they are bound to the body.
“The car companies that give up the battery-swapping mode will use CTC battery-chassis integrated technology,” which is a general industry perception and also becomes a trump card for CTP technology to confront CTB/CTC technology.
This also leads to another topic. The use of CTC/CTB technology means that more charging stations need to be built to solve range anxiety, while the battery-swapping model represents the need to build more battery-swapping stations. The struggle between charging and battery-swapping has once again been placed on the table.
As a player of CTP technology structure innovation, SAIC Mofei battery doesn’t want to argue but wants to “balance,” taking the dual path of exchangeable and chargeable, just like NIO.
Zhu Jun introduced that the English name of Mofang Battery is ONE PACK. As the name suggests, SAIC also focuses on the standardization of “ONE PACK”. The standard battery pack is the basis for large-scale universal battery swapping, which is different from the “standard cell” path proposed by Volkswagen.
At present, there are also differences in the battery swapping lines. NIO’s battery packs with three different capacities can be interchanged, and CATL’s “chocolate swapping block” is a more standardized battery pack with the same size and capacity. However, unlike “chocolate”, Mofang battery packs have a fixed size and a capacity ranging from 40-150kWh. Mofang battery packs of different heights can be interchanged.
Zhang Liang mentioned in an interview, “The biggest feature is still in the battery architecture. The standardized ONE PACK enables our vehicles to be compatible with batteries from 50 degrees to over 100 degrees.” Through the platform-based design unified in size by ONE PACK, and with a separate patented battery swapping structure, MG MULAN can achieve fast swapping of all battery packs on the same device.
Of course, the battery swapping route is not easy. Due to technical, safety and investment return ratio factors, battery swapping has not been fully accepted by the market. CITIC Securities estimated that the break-even point for battery swapping stations is about 20% utilization, which means serving 60 vehicles a day. Currently, it is still difficult for major branded battery swapping stations to achieve this break-even point. Previously, Tesla tried the battery swapping route, but ultimately gave up and turned to the charging route due to the inability to reach the profit point.
However, all success requires development. The breakthrough in the battery swapping market requires joint efforts from upstream and downstream. Perhaps, as Zhang Liang said, “Using battery swapping as an energy replenishment mode, it can be completed in two minutes, which is more in line with consumers’ driving habits than the 15-20 minute fast charging mode.” Compared with fast charging, battery swapping has the advantage of controlling battery performance degradation, “reducing battery degradation to a minimum”.
Difficult tasks always need someone to do it. History often achieves its inevitability through a large number of chances. In the midst of seeking the uncertain times behind the era’s fission, there must always be someone who lights a match to see the road ahead. The battery swapping war ignited by NIO has attracted more and more followers and has entered the spotlight.
However, at present, due to the fact that car companies and power battery companies want to achieve differentiation in the battery swapping market, they have spontaneously come up with different killer points, naturally presenting a situation of each fighting on its own. But this is not a long-term solution, and it is necessary to accelerate the standardization and unification of battery packs as soon as possible. Because once CTC technology matures, the nascent battery swapping model may fall into silence again.
This is destined to be a glorious yet fragile era that requires the power of everyone.
This article is a translation by ChatGPT of a Chinese report from 42HOW. If you have any questions about it, please email bd@42how.com.