Author | Wang Ci
Editor | Qiu Kaijun
“I think I understand manufacturing more than anyone on Earth alive today,” said Tesla CEO Musk in response to a question about Tesla’s manufacturing advantages in a conversation with TED’s Chris Anderson on April 14.
“Musk spent three years living in the Fremont and Nevada factories, fixing production lines, running around the corners of the factory like a madman with the team, and sleeping on the floor,” Musk said.
The three years that Musk referred to were between 2017 and 2019. It was during this period that Tesla achieved mass production, marking the first time in human history that electric cars were being produced on a large scale.
In 2020 and 2021, Tesla’s deliveries approached the thresholds of 500,000 and 1 million vehicles respectively, with the company expected to exceed 1.5 million vehicles this year. In terms of electric vehicle production, Tesla is far ahead of its competitors in terms of scale.
Compared to Tesla’s research and innovation in electric and intelligent vehicle technology and business model innovation, Tesla’s “production mania” ability has always been underestimated.
Tesla not only designs the best electric vehicles, but also produces them most efficiently with the lowest cost – in 2021, Tesla’s automotive gross profit margin was 30.9%, a number that can silence global automakers and shut down those who questioned Tesla’s profitability in the early days.
It is necessary to fully research Tesla’s production manufacturing capabilities, not only to help us understand Tesla, but also to help followers understand that the gap in production manufacturing must be strengthened.
California Factory: Test Base
The California factory that produces two-thirds of North America’s electric cars was a steal for Tesla at $42 million.
In 2010, the automotive industry was still reeling from the heavy blow dealt by the financial crisis. Toyota and General Motors, who previously owned the California factory, were eager to reduce their debt loads, and Tesla luckily acquired the factory for $42 million, which was originally valued at $1 billion.
At the time, Tesla only had one car, the Roadster, which was based on Lotus’s 2,500 chassis. After a simple refurbishment, Tesla put the factory into operation. Since the volume was too small, they made do with what they had.
In June 2012, the world’s first Model S rolled off the production line and was delivered to Steve Jurvetson, a director at SpaceX. At that time, the Fremont factory in California could only produce 60 cars per week.
In 2012, Tesla began producing the Model S at the California factory, followed by the Model X in the third quarter of 2015, the Model 3 in the third quarter of 2017, and the Model Y in 2020.
Before 2017, Tesla’s annual production was less than 100,000 vehicles, which was not much of a challenge for the California factory. Furthermore, in the early days, Tesla did not pursue quantity and did not design cars that were too difficult to produce.
However, some of the drawbacks of the California factory gradually became exposed during this process. Tesla has also been constantly improving the factory.
The factory emphasizes optimizing logistics and transportation to shorten the route, reduce costs, and increase efficiency as much as possible. However, the distance between the stamping workshop and the welding workshop, welding to painting, and plastic parts to final assembly are quite far from each other based on the original factory layout. This kind of workshop arrangement is obviously unreasonable.
Tesla has been upgrading and renovating the California factory to support production growth.
In 2014, the number of employees at the California factory reached 2,000, and half of the area was optimized and put into use, with a more compact workshop layout, resulting in an improvement in production efficiency.
However, three years later, the California factory faced unprecedented challenges after being patched for so many years.
In April 2016, Tesla’s first mass-market Model 3 was released in the United States. The new model was released and 400,000 orders were placed online in just 20 days. Tesla encountered a happy problem – so many orders. It was worth noting that Tesla’s annual production capacity at the time was just over 70,000 vehicles.
The difficulty of mass production was beyond imagination. The three years from 2017 to 2019 when Musk slept in the factory were the three years when Tesla’s California factory climbed up the production slope.
At the beginning, Musk hoped to achieve ultimate automation in the factory and use machines to produce machines. Tesla designed a highly automated production line with more than 1,000 robots and assembly machines, and robots participated in stamping production, bodywork, painting, and assembly. Moreover, the Model 3 was a mass-market model that had to be substantially reduced in cost and reduced in labor expenditure. However, the actual effect was far from the expected result.
In 2016, Musk stated that Tesla could produce 20,000 vehicles per month by the end of 2017. However, in the fourth quarter of 2017, the California factory only produced 2,425 Model 3s.
Musk had to admit that he was wrong. He responded to the criticism on Twitter, saying, “Yes, excessive automation at Tesla was a mistake. To be precise, my mistake. Humans are underrated!”
Tesla made adjustments and replaced some of the full automation with semi-automation and manual assembly. In the end, the automation level of the Model 3 assembly production line remained as high as 95%, including transportation, loading, and component welding.
In 2018, Musk took over the factory. In response to questioning, he said, “As CEO, my job is to focus on the most critical aspects, namely the current production of Model 3.”
In order to improve the production capacity of the Model 3, Musk and his team lived in the factory, working overtime day and night. In 2018, Musk also set up a simple tent assembly line around the California factory, finally achieving the goal of producing 5,000 vehicles per week, and the production capacity reached more than 200,000 vehicles that year.
However, producing 5,000 cars per week is not enough for Musk. His solution is to revolutionize car production by continuously improving production efficiency.
The launch of Model Y carried Tesla’s innovation. In 2020, Tesla announced that it would use an innovative integrated casting technology to directly cast the rear floor of Model Y, which was originally composed of 79 components, into one piece, greatly improving production efficiency.
In the traditional stamping process, presses with a capacity of around 2,000 tons are often used. Tesla has designed the world’s largest press with a capacity of 6,000 tons, which is unprecedented in the automotive industry. This press was first used in the California factory.
In addition, Musk continues to promote automation with more robots on the production line for Model Y.
In addition to producing cars, the California factory also built a 4680 battery test production line.
The 4680 battery is larger in size than the 21700 battery previously used by Tesla, which will increase range by 54% and reduce costs by 56%.
In January of this year, the 1 millionth trial production 4680 battery was produced in the California factory. The product testing report showed that the pass rate of the 14 trial production lines reached 92%, which basically met the minimum standards for mass production. Mass production will begin at the newly opened Berlin and Texas factories at the end of this year.
Moreover, Tesla built a seat factory near the California factory because it was unsatisfied with the quality of supplier seats.
As Tesla’s first super factory, the California factory has served as a test site for many functions and inevitably has problems such as lack of engineering and production experience. Under Musk’s crazy technological innovation and upgrade, the annual capacity of the California factory has increased to 600,000 vehicles, but it is still unable to meet the huge market demand.
However, in the California factory, Tesla has undergone a qualitative transformation from small-scale to large-scale production.
Shanghai Factory: Annual Delivery of Over 480,000 Vehicles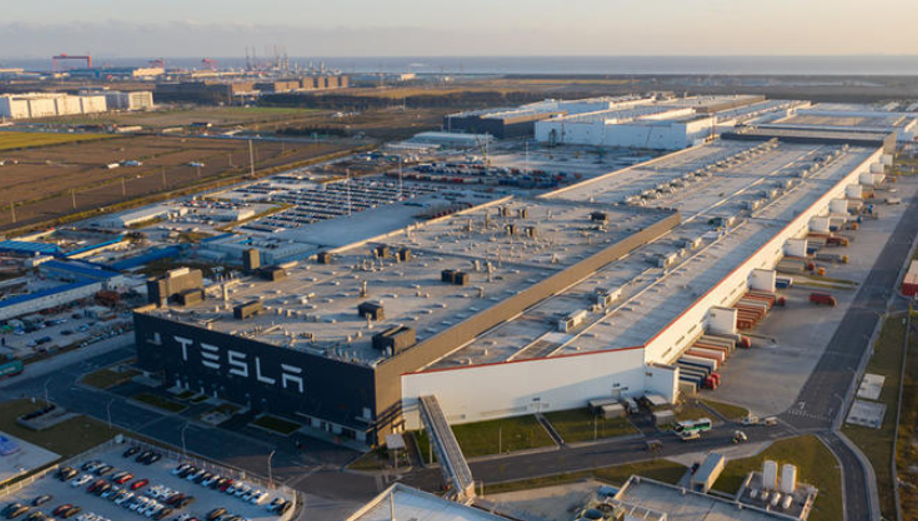
Tesla has to expand its territory and cannot just rely on factories in the US. Its first stop in going global is its biggest market – China.
In the eyes of Chinese local governments eager to attract investment, Tesla has won everyone’s favor. Finally, Tesla chose Shanghai.
The Shanghai municipal government not only provided special land and tax policies to attract Tesla, but also gave the green light for construction. Within one year in 2019, the factory was completed and put into operation, writing a myth of complete automobile factory construction.
The Tesla Shanghai Super Factory is located in Lingang Heavy Equipment Industrial Zone, the southernmost part of Shanghai, and covers an area of 1,200 acres. Although it has only half the area of the California factory, it delivered 484,000 electric cars in 2021, accounting for 51.7% of Tesla’s total global deliveries, which demonstrates its production efficiency.
Standing on the shoulders of the California factory, the Shanghai factory had a smooth ride.
After adopting the validated processes of the California factory, production output rapidly increased.
For example, the stamping process is the same as in the California factory, and the Shanghai factory also uses the world’s largest 6,000-ton high-pressure die caster.
The welding and assembly workshop still pursues high automation, with over 500 KUKA industrial robots working simultaneously. The high-density setting reduces the length of the entire production line, which requires very high demands on overall control procedures. The automation rate of the entire welding and assembly workshop exceeds 95%, which leads the entire automotive industry.
The Shanghai factory also has an innovative feature – Tesla’s unique logistics and warehousing system, which uses containers as mobile warehouses to replace traditional logistics departments, and various materials can be directly sent to the production site. This logistics model does not require additional land space and is more flexible and efficient.
Tesla Shanghai Gigafactory is currently only a first-phase project. The second phase has begun construction and will focus on producing the Model Y, with an expected production start in April 2023. By then, the annual production capacity is expected to gradually increase to 850,000 vehicles.
In addition, Tesla Shanghai is also striving for localizing its supply chain. Musk has previously stated that it is expected to achieve 80% localization at the end of 2020, and costs continue to decrease.
Recently, it was reported by the media that Tesla will establish a second factory in Shanghai, adding 450,000 production capacity and making Tesla Shanghai the “largest automotive export hub” in the world.
The Shanghai plant is almost the fastest-built and fastest- volume production factory in the history of the automotive industry. However, Tesla’s technological innovation has always been on its way, and the technology at the newly completed Berlin and Texas factories is even more advanced with stronger production capabilities.
Tesla Berlin Gigafactory: Groundbreaking Technology
Musk danced embarrassingly again.
In September 2021, Tesla Berlin Gigafactory officially opened, and Musk excitedly danced at the Model Y delivery ceremony.
In October 2021, Tesla Berlin Superfactory held an open day. Afterwards, a video of the factory filmed by a drone for about three minutes was circulated, shocking the industry.
In addition to conventional processes, there are three major technological innovations that are extraordinary: Integrated Pressure Casting Technology, 4680 Cells, and CTC (Cell to Chassis) Chassis Structure.
The first highlight is Integrated Pressure Casting Technology. Unlike the California and Shanghai factories, the production of the Model Y front floor using integrated casting has been realized, further improving production efficiency.
The integrated casting technology for the rear floor has been applied at both California and Shanghai factories.
After the combination of the front and rear integrated casting body and the battery pack, it becomes the unprecedented structural frame designed exclusively for electric vehicles shown in the following image.
The new structure has high structural strength and the cell arrangement is more concentrated, which reduces the vehicle’s moment of inertia and is more beneficial for handling and steering response. The combination of three factors has achieved a 10% reduction in weight and a 14% improvement in range. Even more impressively, this structure reduces 370 vehicle body parts and significantly reduces the production manufacturing process by putting hundreds of industrial robots out of work.
The second highlight is the 4680 cylindrical cell factory.
After the trial production of 4680 cells at California factory, Tesla is now building cell factories in Berlin and Texas to directly supply automotive production factories. The planned capacity of the Berlin cell factory is very large, and Musk said that the battery factory will become one of the largest battery manufacturing factories in the world with an annual production capacity of over 100 GWh, and even potentially 200-250 GWh.
Of course, in the short-term, the battery factory needs to achieve mass production. It is expected to reach a production rate in the second quarter and is estimated to achieve a temporary target of 20 GWh in conjunction with Berlin’s automotive capacity.
The third highlight is the first application of the CTC technology.
“There is no need to put another box in the box.” Musk’s inspiration comes from aircraft fuel tanks. In early aircraft designs, a fuel tank was placed in the wing, similar to how electric vehicles have a battery pack placed on the chassis today. However, this design does not utilize space to the fullest. Later designs directly integrated the fuel tank into the wing, turning the wing itself into a fuel tank.
When the Berlin factory’s CTC technology meets the 4680 cells, the possibilities of extreme manufacturing are limitless. The goal for the end of this year is to produce a Model Y body in just 45 seconds.
For Tesla, the launch of the Berlin factory is of great significance. Musk has inserted a sharp knife into the birthplace of the automotive industry in Germany, and with radical technological innovation, challenged other automotive brands such as Volkswagen and BMW.
But that’s not all. The newly built Tesla Texas factory will become a “machine that manufactures machines” on a cosmic scale.
Texas Factory: The Largest Single Building in the World
On December 1st, 2021, Tesla headquarters moved from California to Texas.
After the completion of the Tesla Texas factory, Tesla’s move to Texas was expected. For Tesla, the Texas factory is crucial.
Construction began in May 2020, covering 12,000 acres, five times the size of the California factory, ten times that of the Shanghai factory, and nearly three times that of the Berlin factory.
Musk mentioned that the Texas factory is the largest single building in the world, so large that it can accommodate 194 billion hamsters. If you stand the factory upright, it is even taller than the Burj Khalifa in Dubai (which is 828 meters high).
In April 2022, the Texas Super Factory began production and delivery, showcasing its stunning production capacity to the world.
The manufacturing approach of the Texas Super Factory is similar to SpaceX’s efficient and low-cost rocket production, with its secret being highly vertical integration. As many components as possible are produced under one roof, reducing logistics and facilitating process adjustments.
Tesla has always referred to its Super Factories as “machine-generating machines,” with the Texas factory being the most advanced and efficient “machine” yet, representing the culmination of its manufacturing capabilities. Musk used the most extreme vocabulary, calling it the world’s most advanced car factory, almost like alien technology.
The Texas factory and the Berlin factory were launched almost simultaneously, and the production process is still innovating.Before the body assembly workshop, there are both stamping parts and integrated die-casting parts. The technology used in the integrated die-casting parts is the same as that of the Berlin factory, which just opened last month, and there is no technological upgrade for the time being. However, according to Musk, in the future, a 8,000-ton die-casting machine may be used to cast larger parts, which will be applied in the electric pickup truck Cybertruck. It is expected that Tesla will be able to achieve one-time die-casting molding of the front and rear body.
In the Texas factory, Tesla’s 4680 battery cell manufacturing process and CTC arrangement technology are also upgraded.
First of all, the encapsulation method of the bottom cover of the 4680 battery cell has been redesigned, which may be for easy exhaust in extreme situations, making the design safer. At the same time, after the battery is scrapped, it is also easy to recycle raw materials.
In addition, the Texas factory demonstrated that the 4680 battery cells were combined into two columns, with 12 sets in total, forming a battery pack.
The battery pack was also displayed.
It can be seen that the 4680 battery cell arrangement in the Texas factory has been improved and upgraded compared to that in the Berlin factory. The battery cell layout is more like the structure of Model 3/Y, with 4 zones arranged longitudinally and a gap in the middle. Each of the two columns consists of 34+35=69 battery cells and a temperature control pipe. Each zone has 69*3=207 battery cells, and the entire battery pack has 828 battery cells. A foam structure about 25 cm wide and a longitudinal gap have been added to both sides, greatly improving safety. This was explained in a video by “wayne’s life” on Xiaohongshu.
In addition, it is worth looking forward to the fact that Tesla will start production of the electric pickup truck Cybertruck, electric truck Semi, and sports car Roadster in the Texas factory from 2023, meeting the demands of the North American market first.
Moreover, Musk stated in his speech at the Cyber Rodeo event in Texas that he hopes to begin production of the first version of Optimus next year. The humanoid robot will better serve humanity and create limitless possibilities.
At the opening ceremony, Musk stated that the main task of the Texas factory in 2022 is to increase production capacity, while 2023 will be a year of new products for Tesla. With the introduction of the Texas factory and the support of efficient layout, integrated die-casting, CTC, and 4680 batteries, the planned annual production of the Model Y alone will reach 500,000, and future production capacity will reach 1 million.
Production Fanatic
If all four of Tesla’s super factories reach full capacity, production capacity will exceed 2.6 million vehicles. In terms of capacity planning and progress, Tesla leads the way among electric vehicle companies.
But don’t underestimate Musk’s appetite.
At the Texas factory groundbreaking ceremony, Musk stated that Tesla hopes to capture over 20% of the global automotive market. This goal is equivalent to twice that of Toyota, currently the world’s largest automaker.
Is this possible?
With Tesla’s reputation as a production fanatic, we cannot underestimate their ambitions. Tesla will undoubtedly continue to expand production and revolutionize the production process.
Tesla is already considering the construction of a fifth automobile factory and may announce the specific location by the end of 2022. In the future, there may be a sixth or seventh super factory, which may be more like alien technology and further disrupt the industry.
Why does Tesla, led by Musk, have such a leading advantage in manufacturing?
(1) Tesla considers manufacturing issues from the design stage, simplifying the design as much as possible for production automation and modularization.
Musk’s favorite saying is “if the process is long, the design is wrong.” If the process is too long, the design is definitely wrong.A typical example is that, in order to achieve higher automation, Tesla has shortened the length of the entire vehicle harness from about 3 kilometers in Model S to 1.5 kilometers in Model 3. Musk even boasted that the length of the harness for Model Y would be less than 100 meters. However, the first batch of Model Y disassembly revealed that the length of the harness was similar to that of Model 3.
Another typical example is the Cybertruck, which has not yet entered mass production. Its design is extremely simplified, aiming to create the easiest car to produce. It has no wipers, turn signal lights, front bumpers, or rearview mirrors. The outer covering is currently a flat stainless steel combination, which is also very easy to manufacture.
(2) Musk rethinks car manufacturing based on first principles, constantly innovating instead of following traditional methodologies.
Traditional automobile production processes have been in operation for nearly 100 years with the standard configuration of stamping, welding, painting, assembly, etc.
However, Musk realized that this model was resulting in too many components and a lengthy production process. Tesla nearly single-handedly developed the integrated casting technology, greatly reducing the number of body parts required.
As for the body of the car, it essentially provides support for the vehicle and requires sufficient rigidity and strength. It is not necessary to produce and assemble several parts if they can be produced by one casting.
The 4680 battery design, production, and assembly also exemplify the use of first principles. The 4680 battery enables the removal of all intermediary links in the application of a power battery, eliminating module and battery pack manufacturing. This is the CTC chassis design, which could reduce the weight of a new vehicle by 10%, increase its cruising range by 14%, and reduce 370 body parts. Undoubtedly, this design also greatly improves production efficiency.
In terms of applying innovative technologies, many automakers may wait for technologies to mature considering automotive safety. However, Musk is different. He boldly applies untested technologies and pushes them forward to maturity. Most of the time, he’s right.
(3) Musk is never satisfied and continuously innovates.
The size of the battery cells has progressed from 18650 to 21700 and then to 4680.
Integrated casting machines, from casting one side of the car body at a time to casting the entire rear of the car, then the front of the car, to casting the entire car body.
California’s attempt to produce with extreme automation failed, but the Shanghai factory continued to improve automation rates. The Berlin and Texas factories continue to improve…
Today, Tesla is a manufacturing madman, but its first car was basically a global procurement effort that was even manufactured in Taiwan before finally being assembled in California. Tesla’s manufacturing starting point was very low, but it now stands alone in the industry thanks to continuous innovation.
(4) Musk’s passion and dedication to production and manufacturing has led the Tesla team to pursue the ultimate in manufacturing. “We like manufacturing.” Musk once said to analysts.
Despite Tesla’s disruptor image, Musk has a profound understanding of automobile manufacturing and a particular respect and understanding for the necessity and difficulty of scaled production in the automotive industry.
Because of this, after breaking through into mass production at the California factory, Musk sent an email to employees saying, “We have become a real car company.”
Reflecting on the days of “production hell” at Tesla, Musk said, “At that time, I slept on the floor so that those team members who were experiencing difficulties could see that I was sleeping on the floor and not in an ivory tower. They would know that no matter what pain they were going through, I was there.”
Employees know that what the boss invests energy into is truly important. In contrast, many intelligent electric car bosses still sleep in ivory towers.
This article is a translation by ChatGPT of a Chinese report from 42HOW. If you have any questions about it, please email bd@42how.com.