The Increasing Burden on Tires
Domestic EVs Enter the Era of Performance Overload
Recently, the IM L7 achieved a 0-100 km/h acceleration time of 3.87 seconds, a 100 km/h-0 stopping distance of 32.69 meters, and a maximum lateral acceleration of 0.968 G in testing at the National Motor Vehicle Product Quality Supervision and Inspection Center (Shanghai).
As a 408,800 RMB electric vehicle, the IM L7 is naturally equipped with rapid torque response, an extremely low center of gravity, 50:50 front/rear weight distribution, and superior front double-wishbone and rear multilink suspension geometry.
However, we must not forget that the four Pirelli tires on the L7 are the only medium through which this 2,290 kg luxury domestic EV contacts the road surface, and they are also the final link supporting the aforementioned performance data.
Electrification’s Demands on Tires?
Due to the differences between EVs and traditional fossil-fuel-powered cars, EV tires need to pay extra attention to the following five technical indicators:
-
Noise
-
Load carrying capacity
-
Durability
-
Traction
-
Rolling resistance
The Quieter the Electric Car, the Louder it Seems?
Electric cars do not have internal combustion engines. Therefore, aside from the sound of electric current, the noise generated by the powertrain of a pure electric vehicle is extremely faint. Road noise, which is usually overshadowed by running noise from the engine intake, fuel direct injection system, valve train, and exhaust system in traditional fossil fuel powered cars, becomes especially pronounced due to the quiet operation of electric motors.To meet the quiet driving experience of electric vehicles, EV tires need to reduce road noise as much as possible. There are various ways to reduce noise, mainly by starting with the sound-absorbing sponge inside the tire, special patterns, and tire formula itself.
Sound-absorbing sponge
When a car travels, the tire is the only means of communication between the car and the ground. As a result, surface irregularities and tire deformation will cause air compression inside the tire, leading to vibration. This vibration will produce noise inside the tire cavity, which is then transmitted to the cabin through the suspension and steering systems or even directly through the air.
To address this type of noise, the solution is simple. Polyurethane sponge should be applied to the inside of the tire. By adjusting the material, density, and porosity of the sound-absorbing sponge, the tire manufacturer can optimize the attenuation capacity of the silent tire for specific frequency vibrations, reducing perceptible noise.
This technology used to only appear in ultra-luxury models such as Maybach. However, in recent years, due to the increase in demand brought by the popularity of electric vehicles and the maturity of technology, this technology has become more popular. Take Pirelli’s P Zero series custom tires, which are standard on IM cars, for example. They are equipped with the Pirelli Noise Cancelling System (PNCS), the yellow sponge shown in the picture above. The sponge itself is not expensive, but what makes it valuable is its coordination with the NVH characteristics of the vehicle to achieve the best noise reduction effect.
Pattern also matters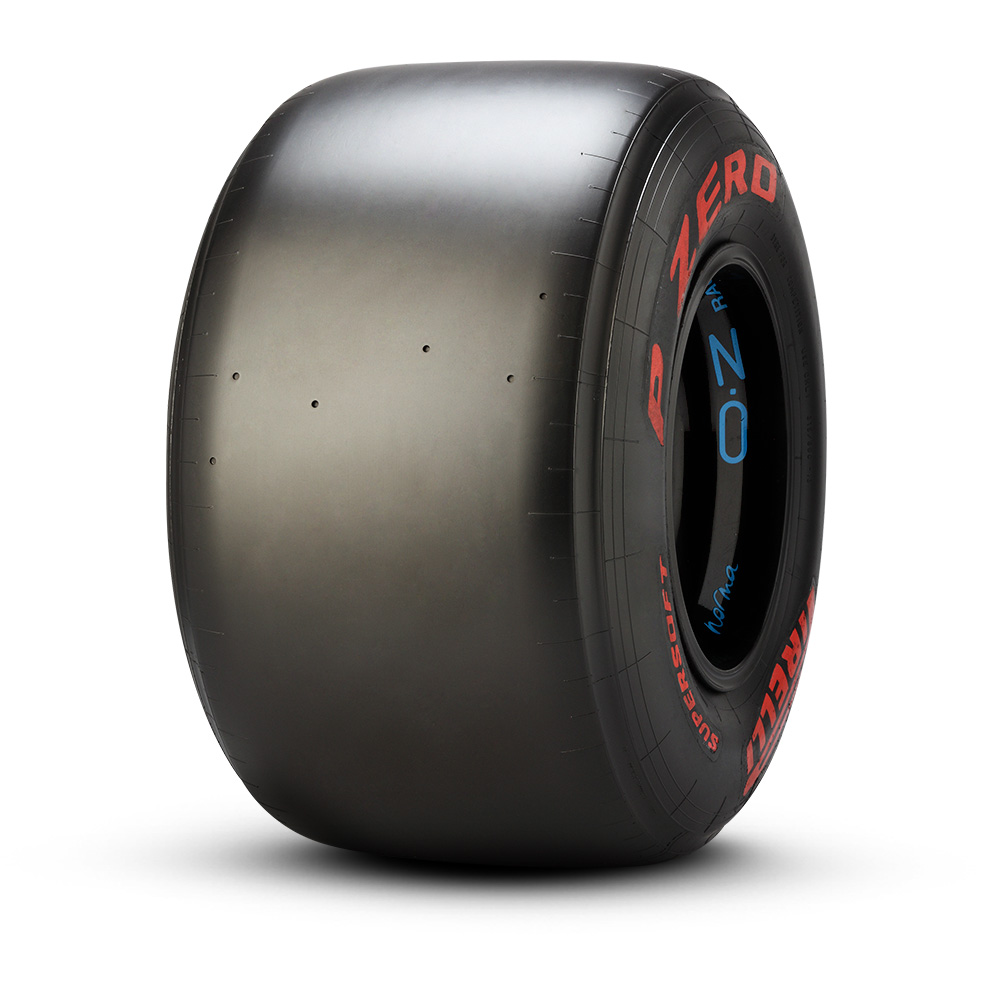
In theory, slick tires used in racing are the quietest tires. However, no one wants to drive a clunky car in rainy weather. Obviously, you need treaded tires to be legal on the road.
However, tire tread is also a major culprit in generating tyre noise. The air between the patterns is compressed and released repeatedly, producing noise.
If the air between the patterns generates noise, reducing the amount of air also reduces the energy contained in this part, thereby reducing noise.
Another way is to use silencers designed based on the principle of Helmholtz resonance to allow the noise generated inside the pattern to cancel itself out.
In addition, by setting columnar protrusions in the groove to scatter sound waves, like a breakwater that breaks the impact of waves, energy can disperse and decay faster.
How to withstand heavy weight and torque?
Tread must grip
The low center of gravity and rapid torque response of electric vehicles have masked the poor movement performance caused by their heavy weight. However, physical principles will not be overturned by the wave of electric power, and the technology of tires is still needed to support the handling of a car.
Apart from simply providing high torque, the reason why electric cars are so fun to drive is because the torque output characteristics of electric motors are completely different from those of gasoline engines, and maximum torque can be instantly obtained without the need to establish rpm.
The sudden surge of torque can cause deformation of the tire surface pattern, thereby affecting the instantaneous transmission of power to the ground and producing hesitation during cornering.
Therefore, the high instantaneous torque places higher demands on the strength of the tire pattern itself. To avoid delaying acceleration due to deformation of the tire surface pattern, performance-oriented EV tires adopt a higher rigidity rubber formula in the center of the tire surface to resist the lateral acceleration caused by power, braking, and heavy weight, and the resulting deformation of the tire surface.
In addition, optimizing the details of the pattern shape also helps to improve performance. For example, adopting an asymmetric and supportive design can optimize the tire surface grip under lateral force and improve steering response.
Finally, the tire surface rubber formula also needs to assist the harder tire surface pattern to ensure higher adhesion.
Strong tire surface and sidewall
In addition to the deformation of each pattern block, the tire surface itself also needs to withstand the greater weight and higher limits of electric vehicles. If it cannot maintain the contact area between the tire surface and the ground, then even the best formula would be in vain.
For example, the Pirelli P Zero on the Polestar 2 uses nylon + aramid in the belt layer, rather than the more common steel wire. It is worth mentioning that the strength of aramid fiber is 5-6 times that of steel wire. As the most common material for bulletproof vests, also known as Kevlar fiber, it is widely used in racing and aerospace fields.
Similarly, in order to prevent deformation of the tire sidewall and the resulting decrease in cornering performance, EV tires also adopt a setting closer to SUV tires and use greater thickness to resist deformation.
How to deal with range anxiety?
Electric vehicles are much more energy-efficient than gasoline vehicles, but carry less energy. This makes the range of electric vehicles extremely sensitive to external factors. Therefore, electric vehicles need to reduce resistance in every way possible, which means reducing rolling resistance for tires.
In short, rolling resistance is the force required to maintain the wheel rolling at a steady speed. Tire manufacturers will roll the tire on a large cylindrical drum and measure the force required to quantify this indicator – the rolling resistance coefficient (RRC).
When the tire rotates, its shape changes, and the part of the tire in contact with the road surface undergoes deformation before returning to its relaxed state. The energy required to make the tire deform is greater than the energy required to restore it to its original shape: this phenomenon is called “hysteresis”. This energy is dissipated in the form of heat.
If you have ever ridden a bicycle with low tire pressure, you will experience hysteresis firsthand. To cruise at a constant speed, you must put more mechanical energy into the system. Compared with inflating the tire to the appropriate level, riding with low tire pressure requires greater pedaling force because low-inflation tires have a lot of hysteresis and produce greater rolling resistance. If you touch the tire after riding, you will find that it is much hotter than when it has air. This is because the energy you used in riding was wasted in the form of heat.
If underinflated tires have high rolling resistance, why not simply overinflate to reduce it? Actually, this can work, but at a cost. On one hand, ride quality is affected. As tire pressure increases, comfort gradually becomes less friendly. More importantly, the higher the tire pressure, the smaller its footprint – the contact area between the tire and the road. A smaller contact area may mean a smaller grip and thus compromised braking and cornering abilities, especially dangerous on wet and slippery surfaces.
Pirelli’s Scorpion Verde (meaning “green” in Italian) all-season tire is Pirelli’s environmentally friendly crossover/SUV tire product line. Pirelli’s technicians faced the challenge of meeting Rivian’s low rolling-resistance target when developing custom tires for the American pure electric pick-up brand.
To meet this demand, Pirelli’s engineers used compounds with high silicon content in the tire formulation to reduce vehicle energy consumption. They also designed the mold specifically to reduce the tire tread pattern and maintain optimal ground pressure distribution, reducing tire-to-ground contact and achieving less energy dissipation.
Choosing the right tire is crucial!
At the end of this tire science article, I must stress again: carbon neutrality is a very big business. Because it represents the trend of the entire industry chain development. There are still many top tire brands that have not been mentioned in this article, as well as many novel technologies, and the tire production process is becoming more and more environmentally friendly. However, due to space and content planning, not all of this information has been presented one by one. Although this is the case, I still believe that everyone now has a preliminary understanding and awareness of energy-saving tires or electric vehicle-specific tires.
Here is the translated Markdown text:
Finally, I would like to answer a long-standing question in everyone’s mind: why do original equipment manufacturer (OEM) certified tires cost so much more than aftermarket tires?
First, it is true that the business model of tire manufacturers in this area will result in higher prices for OEM tires. However, after all, you get what you pay for, and the premium for OEM tires includes the higher development costs.
OEM tires are developed in cooperation between tire brands and automakers from the beginning of chassis development. Regardless of the formula, size, or the matching of softness and hardness in different areas of the tread surface, and other technical indicators, they are the most suitable configuration that conforms to the development of a vehicle’s overall performance and product planning. Although aftermarket tires may be cheaper, they are likely to cause side effects such as uneven wear, increased energy consumption, and reduced comfort. Especially for electric cars with high torque, weight, and sensitivity to range, if the owner wants to experience 100% of the original balanced performance, OEM tires are clearly the most suitable choice.
This article is a translation by ChatGPT of a Chinese report from 42HOW. If you have any questions about it, please email bd@42how.com.