For me, who only started paying attention to LI upon the release of C11, “the king of cost-effectiveness” was my first impression of LI. Although I knew a little about LI’s self-research concepts, I did not pay too much attention to them.
When LI’s sales frequently made the rankings and began to enter the first group of new forces, I still believed that it was only a victory of the “cost-effectiveness” strategy.
However, after seeing the launch event of LI’s CTC battery-chassis integrated technology today, I realized that it was not as simple as just the price.
-
Compared with traditional solutions, battery layout space has increased by 14.5%, and the vertical space of the vehicle body has increased by 10 mm;
-
The torsional stiffness of the vehicle body has been increased by 25%, reaching 33,897 Nm/deg;
-
LI C01 will be the world’s first mass-produced CTC car;
-
In the future, it can be compatible with 800V platform and 400kW fast charging;
-
LI CTC will be open for sharing free of charge, without new technology creating new barriers.
For a company that pursues such high technology, LI, which is believed by people to have taken the low-cost route, is completely different. As the automobile company with the broadest range of self-research after self-proclaimed Tesla and BYD, LI should not only have a low-price label.
Therefore, today we will take a look at LI and its CTC technology that was released today.
Why CTC is Necessary
The focus today is, of course, the protagonist of the technology release conference: CTC battery-chassis integrated technology.
But to talk about CTC, we must first start with CTP, even traditional battery packs.
To address people’s concern about the range, the idea at the level of power batteries is to let the battery “store” more energy. Decomposing it, the material level and engineering structure aspect are involved. In the short term, there will be no breakthrough progress in battery materials, and energy density is difficult to significantly improve, so engineering optimization has become an important point to enhance capacity, that is, optimizing space and fitting more battery cells.
The battery pack form in the early development of electric vehicles is also the form currently used by mainstream electric vehicles, which is the standardized modular battery pack. Simply put, it is like putting an elephant into a refrigerator in 3 steps:
-
First assemble the battery cells into modules;
-
Then assemble several modules together, add a shell, and form a battery pack;
-
Finally, package the battery pack on the vehicle body.The existence of modules makes it easier for battery packs to meet overall technical requirements and assembly needs. However, the obvious disadvantage is that modules and casings occupy a larger volume, resulting in low space utilization. This led to the development of CTP (Cell To Pack) technology, also known as module-less technology, where battery cells are integrated directly into the battery pack, reducing or eliminating the need for battery modules, and integrating battery packs into the vehicle floor as a structural component.
The advantage of CTP is an increased volume utilization rate, a reduced number of parts, and improved production efficiency. The industry’s current development level is in the process of transitioning from standard modules to CTP technology. The disadvantages are collision safety, heat management, and after-sales maintenance. Representing companies currently using CTP technology include BYD, CATL, and Contemporary Amperex Technology Co.
For example, Contemporary Amperex Technology Co’s CTP battery pack results in a 15-20% increase in capacity utilization rate, a 40% reduction in the number of parts, a 50% improvement in production efficiency, and a 10-15% increase in energy density.
CTC (Cell To Chassis) technology is the integration design of batteries, chassis, and lower body, which further simplifies product design and production processes. By reducing redundant structural designs and effectively reducing the number of parts, while improving space utilization and specific energy, the body and battery structure complement each other, thereby greatly improving the battery’s shock resistance and vehicle torsional rigidity.
However, this also means that CTC technology is highly dependent on the R&D of the vehicle chassis. Compared to standard modules and CTP, it requires greater R&D capabilities of whole vehicle enterprises, and more involvement in battery pack design.
In terms of development progress, Tesla released the 4680 battery cell and CTC technology at Battery Day in September 2020. In April of this year, Model Y using CTC technology was officially launched and delivered at the Texas factory. In early July 2021, at the strategic development conference hosted by Volvo and Volkswagen, both traditional car giant companies also made CTC a key technology route. Contemporary Amperex Technology Co previously stated that it will launch CTC technology in 2025.
Meanwhile, the low-key Zeekr has already released its own CTC technology and claimed that the Zeekr C01 will be the world’s first sedan equipped with CTC technology, making it a leader in domestic CTC technology.
Technical challenges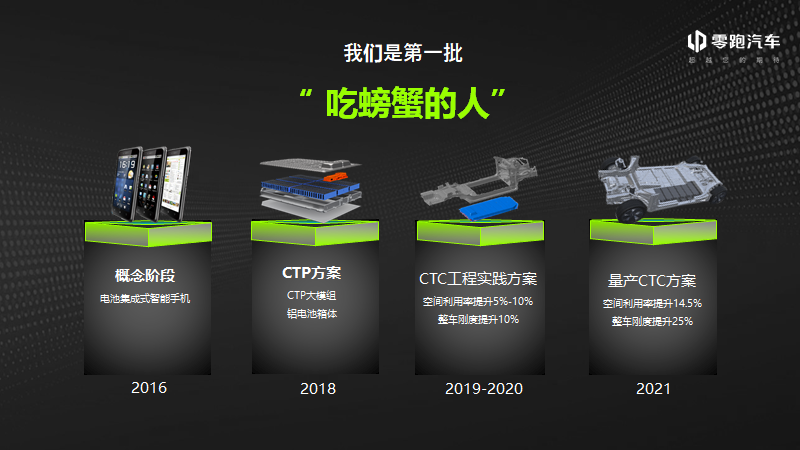
According to the presentation at the press conference, the idea of integrating the Zero Run battery system came from the CEO Zhu Jiangming’s inspiration from smartphone battery design in 2016. At that time, the idea of integrated design was proposed.
It is said that Mr. Zhu formed a cross-departmental project team and personally supervised the project progress. After years of R&D accumulation, the R&D team has overcome 32 key technologies in terms of structure, design, verification, process, and tooling. After overcoming many difficulties, the seeds planted by Zero Run in the early years finally sprouted.
Compared with traditional electric vehicle battery packs, the CTC technology has a significant difference in structure, and the biggest challenge is to be both integrated and relatively modular. In order to solve this dilemma, the Zero Run R&D team proposed an integrated battery chassis structure, which solved two major technical difficulties:
- In terms of structure:
The battery and chassis are integrated in design, and the CTC double-skeletal circular beam structure is innovatively applied, which integrates the battery skeletal structure and the chassis body structure. It is both a vehicle body chassis structure and a battery structure, and the overall structure efficiency is higher.
- In terms of airtightness:
The battery is sealed through the vehicle body design. The CTC technology uses the basic structure of the chassis to utilize the longitudinal and transverse beams of the vehicle body to form a complete sealing structure, which is a great innovation compared to traditional cars.
Technical effect
From a technical perspective, there is a significant improvement in space, endurance, performance, and safety.
The more integrated battery structure has released more precious chassis space. The overall battery layout space has increased by 14.5%, and the vertical space has increased by 10 mm. Don’t underestimate this 1 cm distance. For the limited headroom of a car, every inch is precious.Regarding the mileage of the vehicle, the higher battery space utilization not only accommodates more batteries to increase the mileage by approximately 10%, but also improves the battery’s insulation performance, buffering the power loss defects in winter and further guaranteeing winter driving experience.
In terms of the vehicle’s performance, the torsion stiffness has improved by 25%, reaching up to 33,897 Nm/deg, which can provide better driving performance, excellent handling, and better responsiveness. In addition, the higher the stiffness of the body, the stronger the ability to resist resonance, and the better the NVH performance.
Moreover, in conjunction with the AI BMS developed by LingPao, which combines BMS and cloud platform online & offline, and integrates big data and AI deep learning tools, more proactive protection functions are achieved.
In addition, LingPao’s CTC technology has good compatibility and scalability. It can quickly and flexibly mass-produce and adapt to different platforms and levels, and will also be compatible with 800V high-voltage platforms, supporting 400 kW ultra-fast charging in the future.
In summary, LingPao’s CTC technology is hard-won and deserves recognition.
Self-developed sentiment
If you think the story ends here and that LingPao relies on CTC to form a technological barrier and occupy market advantage, then you have a narrow mindset. The development of new energy vehicles cannot be achieved in isolation, and industry growth is not the work of one person or one company.
During the press conference, Zhu Jiangming announced that “LingPao will share its CTC technology for free.” What a commendation: “New technology should not be a barrier but a ladder to drive industry advancement.”
The rapid development of electric vehicles has given China’s auto industry a chance for overtaking & surpassing their rivals. Behind this opportunity, it is not opportunistic but is the hard work of countless Chinese engineers throughout the entire industry chain. In terms of research and development, LingPao advocates self-reliance. Zhu Jiangming stated that LingPao has become the automaker with the widest range of self-reliance after Tesla and BYD.
Zhu Jiangming blandly said during the press conference that “everything, except for the battery core, is self-developed.” It sounds magnificent, but in practice it’s remarkably difficult. Against the national emphasis on independent technology and scientific self-reliance, LingPao’s difficulties and efforts in self-development are worth being noticed.
ConclusionIn my opinion, LI is like a diligent and pragmatic engineer who doesn’t like to talk much, just like LI’s founder, Zhu Jiangming.
There are no fancy marketing techniques, but they have been persistent in technology. Even the assisted driving chip is self-developed, which is quite “unconventional” in the current automobile industry.
Of course, LI’s “self-developed” is not perfect. Limited by self-development, many basic work needs to be done personally, starting from scratch. As a result, the initial product completion rate is not high. For example, the assisted driving is not very user-friendly, and the high power consumption is often criticized. However, as long as they persist, all problems will eventually be solved. Self-developed capability is the key to solving problems and the guarantee for the steady and long-term development of the company.
Finally, looking forward to the first mass-produced sedan with CTC technology, LI C01.
This article is a translation by ChatGPT of a Chinese report from 42HOW. If you have any questions about it, please email bd@42how.com.