Author: Zhu Yulong
After Oliver Blume sorted out the ideas, he reconsidered many of Herbert Diess’s decisions. As of now, Volkswagen has established its global battery business, PowerCo, which is to some extent a demand of the German automotive industry. With Porsche separating from Volkswagen, PowerCo will also operate independently in the future, responsible for both Volkswagen’s global battery business and the entire battery value chain. From the current positioning, PowerCo will be responsible for managing the operation of global battery factories, battery technology development, vertical integration of the value chain, and the supply of battery production equipment.
Personally, I think Volkswagen’s battery production has received support from Germany and the EU. Although the group has changed its flag, it still needs to continue producing batteries. Recently, PowerCo has started to make efforts towards becoming a global battery champion, as evidenced by the release of “Building a Global Battery Champion”.
With the United States through IRA allowing several automotive companies to participate in the construction of battery factories, PowerCo covers every aspect and is, apart from Tesla, the earliest decision made by European and American car companies for battery production. Actually, not only the development and manufacturing of batteries, but also around industrial expansion, vertical integration of the industry chain, manufacturing equipment, and energy storage systems, PowerCo has ambitious plans with the support of Germany and Europe.
Volkswagen’s Plan
Volkswagen’s future power batteries will mainly revolve around the MEB (MEB EVO) and SSP large-scale platforms, essentially non-vehicle-mounted batteries, which PowerCo also plans to produce. PowerCo’s energy network products are mainly in energy storage battery systems, electric boats, electric commercial vehicles, and other transportation vehicles.“`markdown
For an affordable pure electric car, the battery cost accounts for 40% of the total vehicle cost. The battery material cost occupies 70-80% of the battery BOM cost, and the battery raw material cost occupies 40% of the battery material cost.
Vehicle manufacturers producing batteries, on one hand, guarantee production quantity around the manufacturing process, and on the other hand, take control of the battery supply chain. Volkswagen PoweCo has already prepared in the global raw material supply chain (mining, beneficiation, and purification) by signing LTAe contracts with different companies and combining investment to support PowerCo’s battery production from 2025 to 2027, and vertical integration measures will be taken to reduce costs after 2027.
PowerCo’s first factory is located in Salzgitter, Germany, with a production capacity of 40GWh. Starting in 2025, Volkswagen plans to invest over 20.3 billion US dollars in six super battery factories in Europe by 2030. The annual production capacity in Europe will reach 240GWh, which is enough to produce three million pure electric vehicles’ batteries annually. Volkswagen is also considering establishing a battery factory in North America.
Unified Cell
Volkswagen adopts a unified cell design using the latest battery specification. LG may have withdrawn from producing the cell casing and not participate in this Unified Cell. With battery standardization, Volkswagen will apply it to over 80% of its upcoming BEVs, replacing not only the original 590 soft pack batteries but also overturning the size specifications of the original cell casing batteries.
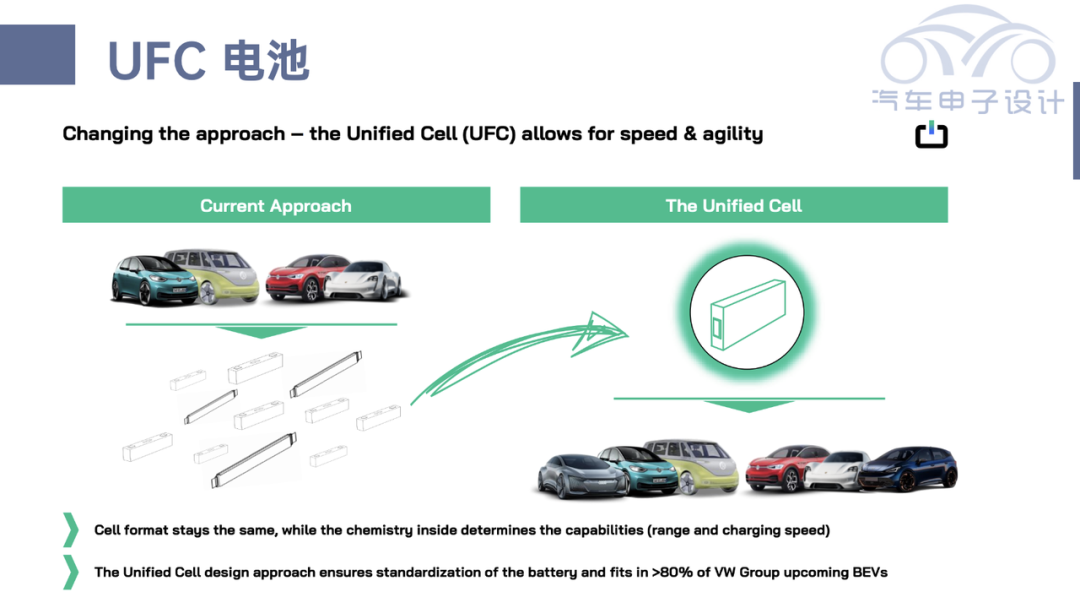
This Volkswagen UFC cell uses the same outer dimensions and structure, differentiated by the cost-effective entry-level battery, the large-scale battery with a balance between performance and cost, and the high-end battery with outstanding performance. This involves the subsequent standardization of battery factories. Volkswagen aims to standardize the production process by using the UFC process to support the subsequent standardized battery factories.
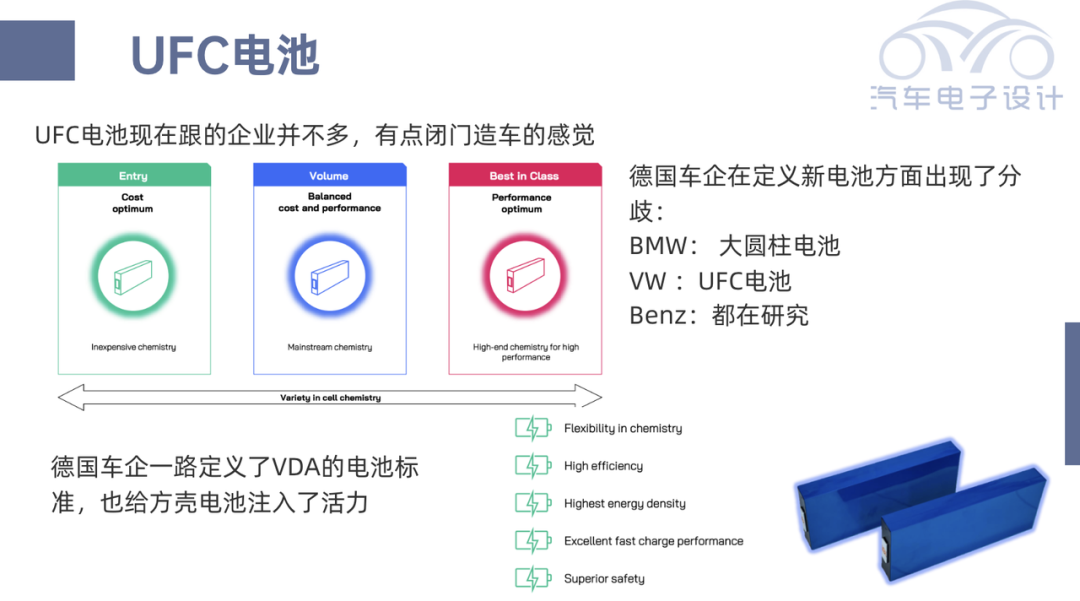
Standardized factories will use standard building column grids to optimize standardization and land use. By designing lean production lines, battery production can cover production advantages. Flexible production configurations allow battery factories to adapt to different chemical compositions and specifications. Single-layer production areas minimize construction time while maximizing flexibility.
This is to prepare for the large-scale expansion of battery factories in Europe in the future.
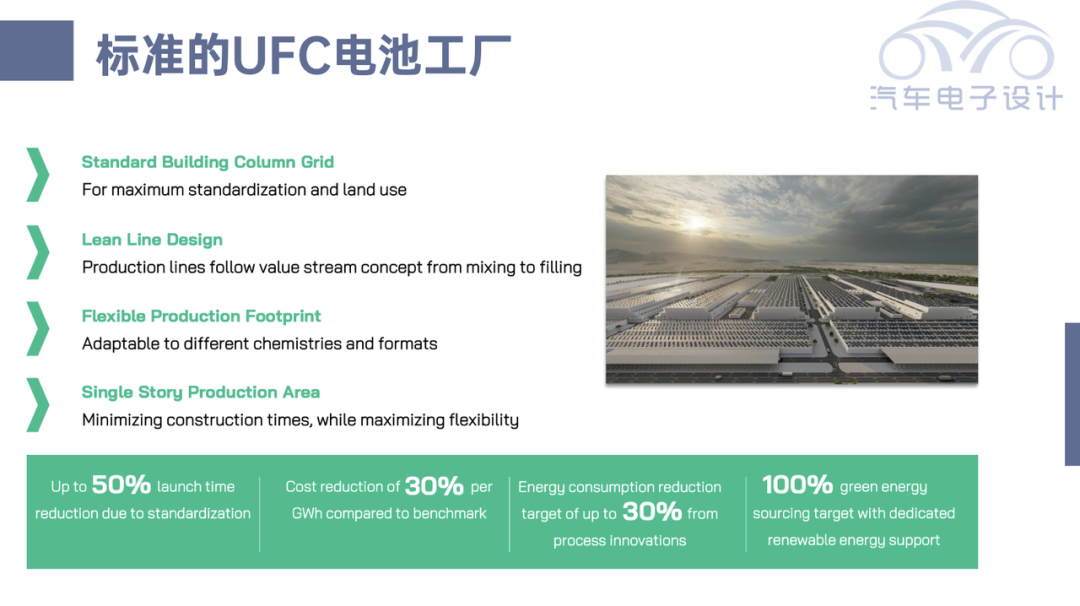
Volkswagen PowerCo and Umicore jointly established a European joint venture to produce cathode materials that will invest 3 billion euros to achieve an annual production of 160 GWh of batteries' raw materials by 2030 and achieve a closed-loop of the entire value chain through recycling.```markdown
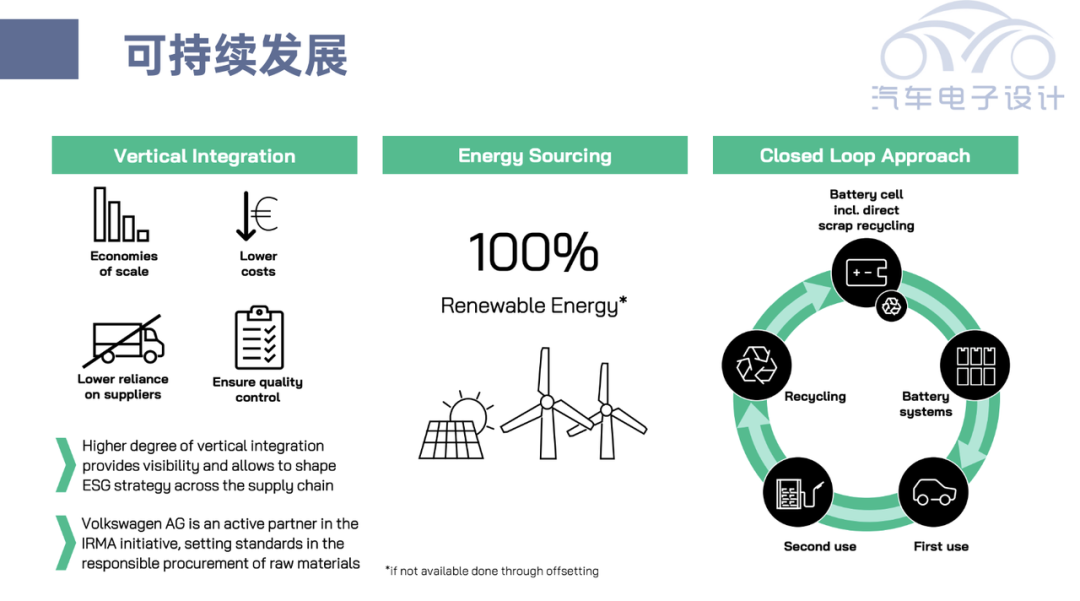
**Summary: Once the man is gone, the tea gets cold. Diess's impact is mainly concentrated in software and vehicle development; in the field of batteries, Europe has put forward requirements at a larger level. This is a bit like our concerns about chips. Similarly, Europeans are also concerned about batteries, so they really have put in full effort!**
This article is a translation by ChatGPT of a Chinese report from 42HOW. If you have any questions about it, please email bd@42how.com.