Author: MuMin
On May 20th, BYD officially released the CTB integrated battery pack and chassis technology, which was first equipped on the Dolphin model, which also opened pre-sales, achieving “production upon release” technology.
In addition to the CTB technology, the Dolphin also first installed the iTAC technology, rear-wheel/drive-four powertrain architecture, front double-wishbone and rear five-link independent suspension.
The “four first installations” give the Dolphin obvious advantages in aesthetics, safety, handling and efficiency.
From the moment of its birth, the Dolphin has been regarded as a direct competitor to the Tesla Model 3, which is also the first time that the two Chinese and American giant new energy vehicle companies, BYD and Tesla, have directly targeted each other in terms of products.
The biggest advantage of the Model 3 is that it is a car that has been verified by the global market, with very strong competitiveness in overall vehicle technology, intelligence level, and product performance. Therefore, in order to beat the Model 3 in this level of car, the Dolphin must have two supports: technology and product experience.
Let’s see how the Dolphin’s technology and product perform?
Technical priority
Before talking about the Dolphin’s technology, let’s first introduce the Dolphin and its marine family.
The “Marine Network Series” products are an independent product system of the BYD brand, just like the “Dynasty Series”. The difference is that the Marine Network is aimed at a younger market, where “sport, youthfulness, and performance” are the main keywords.
The Marine Network system is divided into two series: the Battleship series and the Marine Life series.
The “Leopard Style” is a product in the Lithium Marine Life series of the Marine Network, with a younger product and a more distinct new energy attribute. Because the Dolphin is built on the e-platform 3.0 pure electric platform.
BYD Dolphin has launched a total of 4 pre-sale models, with pre-sale prices of 212,800-289,800 yuan:
- Standard rear-drive elite version, priced at 212,800 yuan, with a range of 550 km.
- Standard rear-drive luxurious version, priced at 225,800 yuan, with a range of 550 km.
- Long-range rear-drive version, priced at 262,800 yuan, with a range of 700 km.
- Four-wheel-drive performance version, priced at 289,800 yuan, with a range of 650 km.
Based on this price, the main selling model will be the long-range rear drive version, which has a CLTC range of 700 km, which has reached the industry’s leading level. However, competing directly with the Model 3 in this way is obviously not enough. The Dolphin needs to show the market its own technological strength. When it comes to technology, we will start with the CTB, one of the protagonists of the press conference.
Integrated Battery Pack and Chassis Technology CTB
Recently, there have been many disclosures about “integrated battery pack and chassis technology,” including Tesla’s CTC, CATL’s CTP and CTC, and Leapmotor’s CTC, as well as BYD’s CTB.The concept of “CTC” (Cell to Chassis or Cell to Car) usually refers to the integration of battery cells directly into the chassis. Besides CATL’s CTP, other companies who mention “CTC” include CATL’s CTC. Their ultimate goal is the same: minimize packaging components and integrate the cells directly into the chassis to achieve cost optimization. However, the difficulty of this technology makes it almost impossible to achieve ideal engineering status in one step, so companies like Leapmotor, BYD, and Tesla have made compromises. According to “Zhuhua Automotive,” the current mass production plan is essentially the idea of integrating part of the battery system itself structure with the chassis of the vehicle. Leapmotor C01, BYD CTB, and Tesla have adopted three different technical solutions, and from the perspective of technical implementation, Leapmotor’s CTC is essentially the integration of the module into the body, which makes it the easiest to implement. The blade battery itself does not need to be modularized in BYD CTB. Tesla’s structural battery is the most complex. From the perspective of integration:
- Leapmotor C01 has the lowest integration degree, and the module still exists.
- BYD CTB is second, and the battery pack cover is removed.
- Tesla has the highest degree of integration, and the entire battery pack has become part of the chassis.
In terms of changes to the entire vehicle assembly line, Leapmotor’s C01 has minimal changes, followed by BYD CTB, while Tesla’s entire vehicle assembly process has undergone significant changes. BYD CTB not only removes the cover but also integrates the original passenger cabin floor as the cover. The simplified chassis frame on the right side of the presentation slide shows significant changes, but the beam connecting the door sill to the middle of the car body remains, so the battery pack installation solution may not require significant changes.## BYD’s CTB Solution
BYD still faces several challenges with its CTB solution, including sealing performance, thermal control, and the load-bearing capacity of the battery’s top cover.
The biggest difference between Tesla’s Structural Battery and BYD’s CTB is that Tesla has taken a more radical approach. Not only has it integrated the battery pack into the body’s cross members, but it has also directly mounted the seats onto the battery pack. This change makes assembly more difficult and requires very high strength in the connection points.
Considering the technical depth of the entire technology, Tesla’s approach is more thorough than BYD’s, but this is not a simple comparison of the two technologies’ quality. From a mass production perspective, BYD’s approach is evidently easier, while Tesla will face more obstacles. This is also why Model 3 has not yet completed the CTC switch.
In its CTB solution, BYD has used a honeycomb structure to reinforce the overall structural performance. BYD has achieved the following benefits through its CTB technology:
-
The Sea Lion’s body torsional stiffness has reached 40,500Nm/degree, which broadens handling limits and provides an excellent platform for overall vehicle comfort and NVH performance.
-
With the same net height inside the car, the Sea Lion’s body height has been reduced by 10 mm, resulting in a lower, more aerodynamic profile and improved visual effects.
In summary, from the gradual implementation of CTC, the direction of body and battery system technology integration is becoming clearer. The main goal is to achieve the optimal solution for the entire vehicle’s cost and production efficiency through engineering optimization. Despite different degrees of integration between BYD, Zeekr, and Tesla, the goal is the same. Although Zeekr and BYD may not be as extreme, they can be quickly mass-produced, which can also provide a landing strategy for other manufacturers.
This is the technical basis for creating a popular product. However, the question of whether it can become a popular product still depends on the product itself.
Everything is Just Right
“Everything is just right.”
This was the conclusion my friend and I reached when we were discussing the Sea Lion after the launch event. The reason for this consensus is that among BYD’s many new energy products, the Sea Lion is the most electric “pure electric sedan.” This not only refers to the pure electric platform but also to the design.
Oceanic Aesthetics
Exterior Design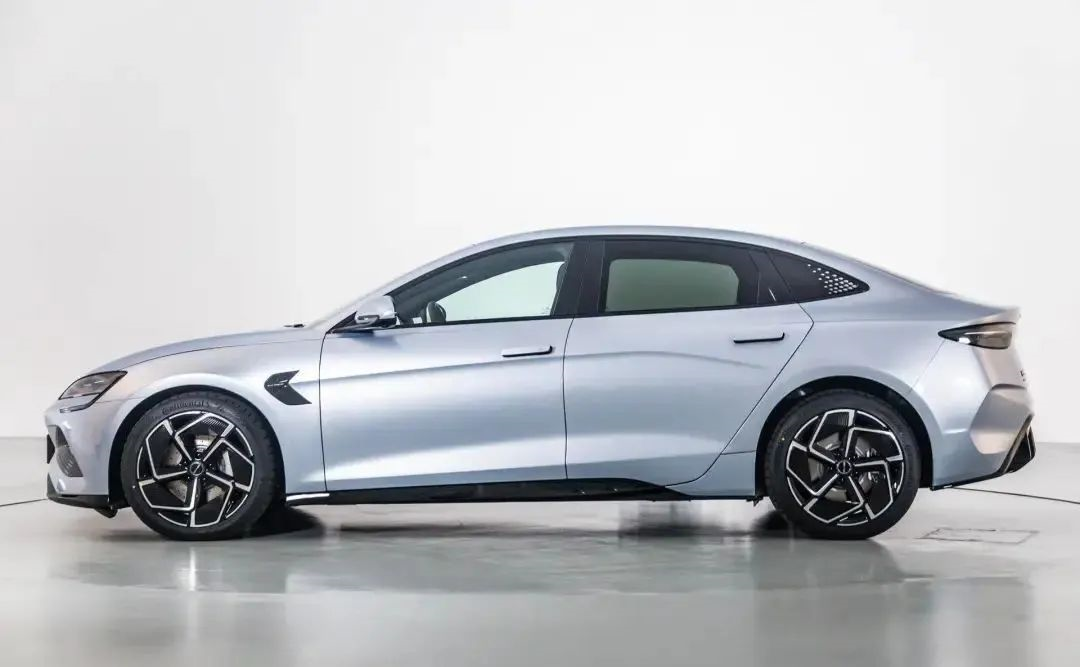
The design team of BYD, led by global styling director Wolfgang Egger, was responsible for the design of the Dolphin. Egger’s designs have always had a wide user base, and with the support of the e-platform 3.0, the Dolphin’s lower body height, low body posture, short front and rear overhangs, and long wheelbase proportions give people an intense sense of motion at first sight.
The Dolphin’s headlight lines are sharp, and the inside of the lamp chamber is a suspended U-shaped LED lighting component. The design of the headlights and the outside of the boomerang-shaped decoration together form the shape of the letter “C,” which is echoed by the turn signal on the side mirror.
The Dolphin features a closed grille design that outlines the letter “X.” Below this are carefully designed aerodynamic components that guide air flow quickly to the bottom of the car.
The dual waistline is a highlight of the Dolphin’s side design. The long and rearward tilting waistline starting from the front wheel eyebrow creates an elegant and luxurious atmosphere unique to static luxury cars.
The Dolphin’s rear bumper is not designed with a simple solid body. The two decorative pieces on either side use dense horizontal bars, which are exquisitely detailed and have a sense of electricity to them. The large black air guide structure in the middle effectively reduces wind resistance.
Interior Design
The interior of the Dolphin takes a completely different approach from Tesla, with a focus on lines. The dashboard divides different functional areas through differences in materials and color.
The position of the A-pillar in the Dolphin is further forward to eliminate the sense of spaciousness of the dashboard. The top of the dashboard features a wave-like shape.
The decorative spines of the steering wheel are in the shape of the Dolphin’s tail fin, adding a playful touch. The multifunctional buttons on both sides of the steering wheel ensure that the driver can complete most operations without taking their hands off the steering wheel.
The Dolphin’s interior is decorated with rhombic stitching and double stitching, further enhancing the overall high-quality and exquisite feel of the interior. It is worth noting that the punching treatment of the interior fabric, in addition to better air permeability, has water droplet-shaped gaps that respond well to the ocean theme.
Compared to the debatable design, the following technology guarantees the playability of the Dolphin.
Performance
- The 550 km standard range rear-wheel drive version of the electric motor has a maximum output power of 150 kW and a maximum torque of 310 N・m.- The electric motor with a maximum output power of 230 kW and a maximum torque of 360 N·m is available for the 700 km long-range rear-wheel drive version.
- The four-wheel drive performance version has a maximum total power of 390 kW and a maximum total torque of 670 N·m. The 0-100 km/h acceleration time is 3.8 seconds.
These data are also excellent for new energy vehicles with excess performance. Compared with such paper-based data, the sea lion is the first to use the rear-wheel drive platform, which is worth being happy for fans who like sports. The car bottom adopts a fully sealed flow guide plate design, which solves the problem of heat reflux in high-temperature environments, improves the efficiency of the cooling system, and reduces air resistance.
The fully sealed flow guide plate also ensures the airtightness between the cooling system and the active drag reduction grille. By automatically adjusting the opening degree of the active drag reduction grille through the control system, only the necessary cooling air is provided for the cooling system, reducing air turbulence in the front compartment and effectively reducing wind resistance.
By optimizing more than 20 parts such as wheel hubs, door handles, wheel flow guide plates, and rearview mirrors, the wind resistance of the sea lion can be as low as 0.219.
Exciting Handling
Independent Suspension with Front Double Wishbone and Rear Five-link
The sea lion adopts independent suspension with front double wishbone and rear five-link, which can bring more driving pleasure. Due to the forging aluminum alloy used in the suspension swing arm and steering knuckle, and the low-friction coefficient high polymer material used in the suspension bushing, the non-spring mass is lighter, and the response to road changes is faster, providing clearer road sense.
iTAC Intelligent Torque Control Technology
The BYD sea lion is the first to be equipped with iTAC Intelligent Torque Control Technology. This technology changes the way of dynamically restoring stability by only reducing power output in the past. It is upgraded to torque transfer and controls vehicle stability through multiple control methods such as appropriately reducing torque or outputting negative torque.
Based on the wheel speed sensor, iTAC adds a motor rotation variable sensor. Compared with relying solely on the wheel speed sensor, iTAC’s identification accuracy is increased by more than 300 times, and it can predict the trend of wheel speed changes more than 50 milliseconds in advance.
In brief, when there is an abnormality in the wheel end but slip has not yet occurred, the system has already identified the abnormal ground force and adjust the torque matching of the wheel end in advance to restore vehicle stability.
When the vehicle is about to slip, iTAC can transfer torque from the wheel end with low adhesion to the wheel end with high adhesion, or output negative torque at the wheel end with low adhesion to enhance the torque of the wheel end with high adhesion, ensuring the extreme case of the entire vehicle’s power output and dynamic stability.iTAC can anticipate power distribution and adjust it in advance based on the integrated status of the vehicle and the driver’s transverse and longitudinal control demands to avoid or reduce the triggering of the ESP, ultimately reducing the amount or suppressing the occurrence of skidding and fully tapping into the vehicle’s power potential, enhancing safety and ride comfort while also expanding the limits of control.
Frequency-variable Damping Shock Absorber
The frequency-variable damping shock absorber is equipped on the Hippo 650 KM four-wheel drive performance edition, which is a semi-active suspension technology.
When the road conditions are good, the damping of the shock absorber is relatively large, making the vehicle dynamics more stable and enhancing its handling; on bumpy roads, the damping automatically decreases, better absorbing the impact of the road and ensuring a high-quality riding experience.
To sum up, BYD has been generous in hardware that can increase the vehicle’s performance and handling in this B-class sporty electric vehicle which, compared with the Han EV, does not need to consider too much about comfort demands. Competing with the Hippo is not about avoiding, but rather about biting a piece of meat from Tesla’s long suit, and can only be achieved through positive competition and surpassing the past.
With a solid hardware foundation, only a real experience is left for us.
Other Technical Hardware
Eight-in-One Electric Powertrain
Different from the commonly used three-in-one electric powertrain in the industry, the Hippo is equipped with a deeply integrated eight-in-one electric powertrain, which integrates the driving motor, transmission, motor control unit, vehicle control unit (VCU), battery management unit (BMS), high and low voltage DC-DC converter, bidirectional onboard charger (Bi-OBC), and high-voltage distribution module (PDU) into one, increasing the power density of the electric power system by 30% and reducing the weight by 16%, with a comprehensive working condition efficiency of up to 89%.
The Hippo’s eight-in-one electric powertrain uses BYD’s self-designed and manufactured flat-wire motor, which adopts ultra-thin high-performance silicon steel sheets, breaking through the industry’s problems of flat-wire motor winding. The slot fullness of the motor is increased by 15%, the wire package is shortened, the use of copper is reduced by 11%, and the resistance is reduced by 22%.
By optimizing the magnetic circuit design to reduce motor iron losses, the cooling performance has been greatly improved, and the rated power output of the motor has increased by 40%, with a maximum efficiency of up to 97.5%.
Battery Pack Coolant Direct Thermal Management
The Hippo employs the industry’s first battery pack coolant direct thermal management technology, using coolant instead of traditional coolant to directly cool or heat the battery, reducing indirect heat exchange losses and improving the temperature uniformity of the battery pack. The temperature difference of the battery pack is controlled within 5°C, improving thermal efficiency by 20%, not only enhancing the overall performance of the battery pack but also extending the battery life.
Wide Temperature Range and High-Efficiency Heat Pump System##Sea Lion with High-Efficiency Heat Pump System
Sea Lion, equipped with a wide-temperature range and high-efficiency heat pump system, achieves efficient temperature control of the battery pack through the direct cooling and heating technology of refrigerant, and can also control the passenger cabin temperature with low energy consumption if needed. The heat pump system can absorb the residual heat of the electric powertrain and operate within a wide temperature range of -30℃ to 60℃.
Compared with the traditional PTC heating device, the heat pump system has a faster temperature control speed, and the winter driving range can be increased by 20%.
Sea Lion’s heat pump system has 11 operating conditions, covering all the scenarios for daily heating and cooling use. Sea Lion is equipped with an active air inlet grille as standard, which improves the heat recovery efficiency of the heat pump system by 20%. As the electric powertrain adopts oil cooling instead of water cooling, the heat recovery efficiency of the heat pump system is further improved.
In extremely low-temperature environments, when the heat absorbed by the heat pump system cannot meet the heating demand of the entire vehicle, the system will generate additional heat energy through intelligent control of the electric powertrain in various modes to meet the needs of the heat pump system. Even in extreme weather conditions of -40℃, the heat pump system of Sea Lion can still start normally and reduce heating energy consumption.
High-Voltage Electric Drive Boost Charging Solution
Sea Lion adopts a high-voltage electric drive boost charging solution, which provides faster charging speed and greatly reduces user waiting time. Based on the development of electric powertrain and charging and distribution powertrain, this technology innovatively uses the motor inductance instead of the boost inductance in the original boosting scheme to meet the high-power DC charging of the 300V-750V voltage range.
Due to the high integration of the system, the motor charging and driving modes are reused during the charging process, and Sea Lion reduces the heat generated by the charging and distribution powertrain, making the performance more reliable. The high-voltage electric drive boost charging solution can fully utilize the current upper limit of the charging pile national standard, realizing a wide-range constant power charging. The full charging time is significantly better than the high-power charging system in the industry, enabling 15 minutes charging for 300 km driving.
This article is a translation by ChatGPT of a Chinese report from 42HOW. If you have any questions about it, please email bd@42how.com.