Fake it till you make it.
In many cases, the first step towards achieving something is to “blow up the cow”. In 2020, Tesla unveiled the revolutionary 4680 battery on Battery Day, only one year after the concept of the 4680 battery was proposed by Panasonic and a European chemical laboratory based on the theory of “Full Coating Ear”. Finally, they believed that the 4680 battery was a good solution after optimizing and improving the cylindrical battery.
If it were Panasonic’s style, at least it would have to wait until 2022 to start publicizing it and it may not start mass production until after 2025. After all, what is made in the laboratory is completely different from mass production. However, Tesla dared to “blow it up” again, and it seems to have succeeded this time.
At the Electric Vehicle 100 Forum 2022 that just ended, Panasonic, BYD Battery, CATL, and other battery giants expressed their favor for the 46-series large cylindrical battery. At the same time, in January, Tesla announced that it had started pilot production of one million 4680 batteries in its California factory, and the official installation of 4680 batteries is already within reach.
Now let’s focus on the core technological innovations of Tesla’s 4680 battery and its future impact on the market.
Understanding the 4680 battery
Before introducing the core technology of the Tesla 4680 battery, let’s get to know the 4680 battery through a few Q&As.
What is a 4680 battery?
A 4680 battery is a cylindrical battery with a diameter of 46 mm and a height of 80 mm. The 18650 and 2170 batteries currently used by Tesla also conform to this naming convention, in which the last “0” of the 18650 battery denotes cylindrical, but the 2170 and 4680 batteries have omitted it.
Why 4680 battery instead of larger or smaller ones?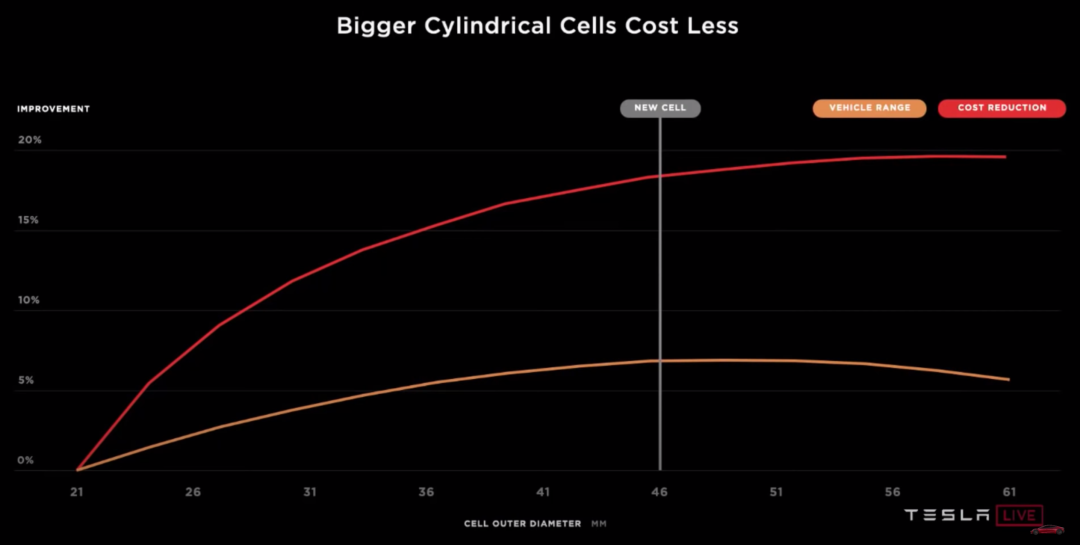
First, let’s consider the “46 mm” diameter indicator. From a safety perspective, while reducing the number of battery cells in the entire vehicle can lower the difficulty of BMS management, the heat dissipation of large battery cells is a challenge. 46 mm is a point within the balanced range. From the perspective of improving range and reducing costs, Tesla believes that the range of the entire vehicle begins to decline beyond 46 mm, and the marginal benefits of cost reduction become very low. Therefore, 46 mm is the optimal solution. In addition, from the perspective of internal stress, 46 mm is also a critical point. Without essential breakthroughs in chemical performance and production processes, 46 mm is a golden size.
Another parameter, “80 mm” height, currently has no consensus in the industry, mainly because chassis designs differ among manufacturers. For example, BMW uses the 4695 scheme, while other manufacturers have planned a 46105 scheme, with a height of 105 mm. However, this height cannot be too high. On the one hand, radial heat dissipation will become a problem, and on the other hand, this will significantly increase the thickness of the chassis, affecting the design aesthetics and wind resistance.
Why is Tesla fond of cylindrical batteries?
Simply put, it is due to “path dependence”. Tesla was founded in 2004 and launched its first model, the Roadster, in 2008. At that time, there were no very mature power battery solutions available on the market. Panasonic’s 18650 battery was already very mature and stable in the civilian sector, with excellent safety and consistency. Therefore, Tesla chose a scheme of assembling thousands of individual cells, which posed a big challenge to BMS, but was indeed more reliable than other power battery solutions at the time.
With the development of power batteries, the 18650 battery has gradually been upgraded to the 2170 battery. Tesla and its suppliers Panasonic, LG Chem, etc., have become more and more specialized in cylindrical batteries. However, this upgrade to the 4680 battery is also a squeezing of the toothpaste for cylindrical batteries.
Toothpaste squeezed, Tesla 4680 battery’s core technological innovation points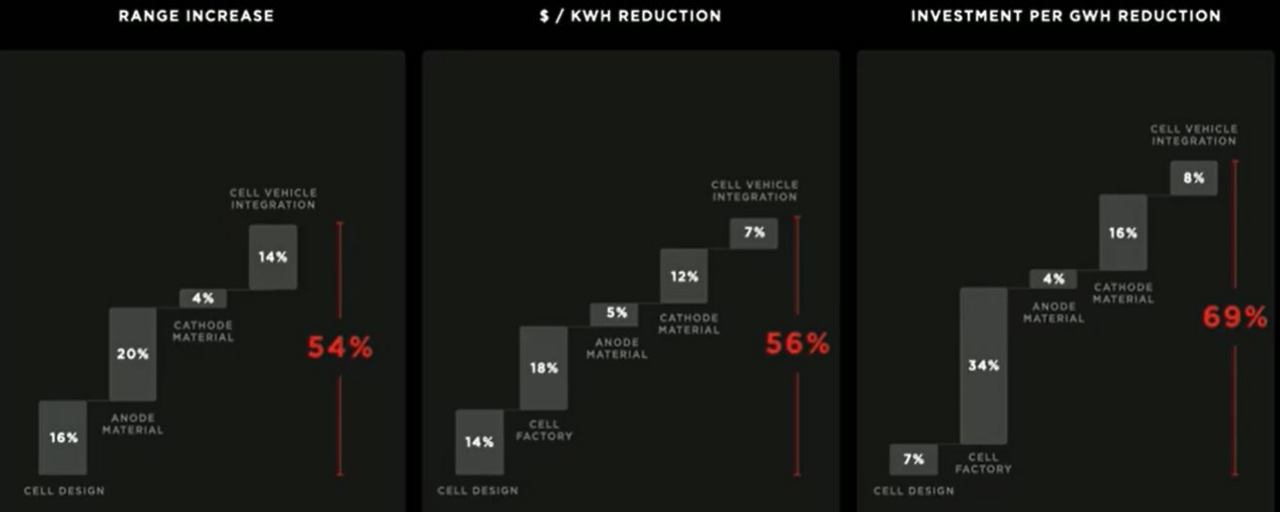
It is evident from the numbers that the upgrade from 18650 to 21700 was quite a squeeze, a bit like the recent Qualcomm Snapdragon chips. However, the 4680 battery is not only 448% larger in volume than the 2170 battery, but also combines revolutionary technologies such as the full-circuit ear technology, high-silicon negative electrode, and CTC combination. As a result, it achieves a “squeeze to the last drop” type of improvement, with a 54% increase in range, a 56% decrease in cost, and a 69% decrease in unit production equipment investment (of course, Tesla’s PPTs have always been a bit exaggerated, and this should be achieved after two or three iterations of the 4680 battery).
Full-circuit Ear Technology: Go Far and Charge Fast
Traditional batteries have a major limitation: energy density and power density cannot be balanced. For example, the energy density of the Honda Accord hybrid’s ternary battery is only 82 Wh/kg, while that of the ternary lithium battery for pure electric vehicles is generally between 150-180 Wh/kg. This is because the core parameter of HEV lithium batteries is power density, as the battery is small (the battery capacity of the Accord hybrid is only 1.3 kWh) but has to drive a high-power motor, some mass energy density must be sacrificed.
However, Tesla’s 4680 battery achieves a balance between the two by adopting the full-circuit ear (Tesla calls it the “no-circuit ear”) solution. The ear is simply the contact point of the positive and negative electrodes during charging and discharging. Traditional batteries have one ear for each electrode, resulting in a problem where the current has to traverse a long horizontal path (as shown on the left side of the above picture) when flowing from the positive electrode to the negative electrode, which increases the internal resistance, not only wasting the battery’s energy but also making heat dissipation difficult to solve.According to Tesla’s patent, the structure of the 4680 battery has evenly distributed tabs on the positive and negative electrodes, which greatly shortens the distance between tabs. For example, the electronic path of 2170 batteries flowing through the entire winding electrode in the current collector is about 900 mm, while the thickness of the positive and negative films of the 4680 battery is 4-5 times that of the 2170 battery. If single tabs are still used, the electronic path will be as long as 3.8 meters, and the internal resistance will also increase by four times. However, the design of full tabs can shorten this path to the height of the battery, which is 80 mm. According to Tesla’s explanation, the heat generated by the internal resistance of the 4680 battery is only one-fifth of that of the 2170 battery. In addition, the full tab solution greatly enhances the current path, making it easier for electrons to move inside the battery.
As a result, the full-tab 4680 battery has the innate ability to discharge at high power and supercharge quickly. According to a research report by Insideevs, a 400V 4680 battery system requires only 15 minutes to charge 70% of its capacity, while the Porsche Taycan and Hyundai IONIQ, which use 800V battery systems respectively, require 18 and 22 minutes to charge. If the 4680 battery adopts an 800V voltage system in the future, charging speed will be even faster.
The key to achieving an energy density of 300 Wh/kg per single unit is high-nickel cathode and high-silicon anode. Currently, Tesla’s 4680 battery cathode still uses the NCM 811 high-nickel solution, which is familiar to everyone. In the future, the 4680 cathode will evolve towards higher ratios of nickel (such as NCM 9/0.5/0.5) as well as “cobalt-free” and “quaternary” solutions. Changes in the cathode are not significant, therefore, the anode is the key to achieving higher energy density. Currently, most batteries use graphite anodes, but the theoretical capacity of graphite is 372 mAh/g, and its actual capacity has already reached about 330-370 mAh/g, reaching its limit. In contrast, the specific capacity of silicon can reach 4,200 mAh/g, which is more than 10 times that of graphite. Therefore, adding a certain proportion of silicon to the anode has always been the direction for breaking through the energy density of batteries.
In fact, Tesla had already introduced the “doping silicon” technology as early as 2017, when the Model 3 equipped with 2170 batteries (supplied by Panasonic) was launched. However, the proportion of doping was relatively small (about 5-6% of silicon alloy), and the improvement in energy density was not obvious. Some domestic manufacturers have also adopted doped silicon negative electrodes. For example, the negative electrode of the battery for the Guangzhou Automobile Aeolus LX with a range of 1,000 km and a capacity of 144.4 kWh contains a certain proportion of silicon. In addition, IM Auto and NIO will also use this technology for the “solid-state” battery with a capacity of 150 kWh that will be put into production in the fourth quarter.
Although “doping silicon” can immediately improve energy density, silicon is inherently less stable than graphite and therefore more susceptible to expansion. Generally, the volume expansion of the carbon-based negative electrode in the process of lithium insertion does not exceed 10%, while that of the silicon-based negative electrode can reach 360%, leading to SEI film damage and other side reactions, resulting in capacity degradation.
Comparatively, the structure of the 4680 battery is more suitable for “doping silicon”. Firstly, the characteristic of cylindrical battery electrode winding can maximally ensure the uniform force expansion of the electrode in all positions, reduce the occurrence of damage and wrinkles. Square and pouch batteries are prone to stress concentration and damage at the corner radius. In addition, the mechanical strength of the stainless steel shell of the 4680 battery is large, which can fully absorb the expansion force of the negative electrode. Therefore, theoretically speaking, more silicon can be doped into the 4680 battery negative electrode, and the energy density is expected to be significantly improved to more than 10%.
CTC technology: A natural ally
From the first principles, to improve the energy density of the battery pack, the fewer “middleware”, the better. To put it simply, if you want to pack as many eggs as possible in a box, it is best to remove the egg tray, which is equivalent to removing the module. In an extreme case, the box can also be removed, which is CTC (Cell to Chassis) technology, also known as CTV (Cell to Vehicle).
The 4680 battery has inherent potential when combined with CTC technology. Firstly, CTC has certain requirements for the structural strength of the battery, which needs to withstand a considerable mechanical load. Compared to 18650 and 2170 batteries, the larger size and higher structural strength of the 4680 single-cell battery are guaranteed through its stainless steel casing instead of aluminum. Additionally, adopting CTC technology eliminates the need for maintenance and replacement. If there is a severe collision or inconsistency in the battery, replacing the battery may be the only option, but cylindrical batteries have always had an advantage in consistency. Finally, compared to pouch batteries, cylindrical batteries have a more flexible layout and can adapt to various chassis. Coupled with the advantages of high energy density and high charge-discharge power of the all-terminal ear structure, their potential in HEV and PHEV fields is enormous.
In addition to the all-terminal ear battery, high-nickel + high-silicon and CTC technology, Tesla’s 4680 battery also has several other technological applications. For example, coating PVDF on the membrane to prevent silicon negative electrode expansion, adding silicon nanotubes to improve conductivity of the negative electrode, and Tesla’s second-generation 4680 battery may use the process of dry electrodes. In short, Tesla is squeezing out all the toothpaste, it remains to be seen how competitors will respond.
4680 Cylindrical Battery vs CTP Square Battery, Is CATL in Danger?
Data shows that since 2019, the square battery has accounted for about 80% of China’s power battery market, with CATL occupying more than half of that market share. The 4680 battery’s first target is, of course, CATL.
Here, we put aside soft pack batteries mainly used by European customers such as Mercedes-Benz and focus on comparing the strengths, weaknesses and development trends of the CTP square battery and the 4680 cylindrical battery.
First of all, in terms of the grouping efficiency of square batteries, it is obviously superior to cylindrical batteries, and it is expected that excellent CTP square batteries can reach 80% to 90%, while 4680 + CTC can reach over 70%. This is not difficult to understand. Although the 4680 battery is much larger than before, it is still much smaller than large square batteries. A Model Y requires approximately 960 4680 batteries, while only 6 to 10 square shells may be required. The fewer the quantity, the lower the proportion of other parts unrelated to chemicals.
However, due to the large size and surface contact of the square battery monomer, it is difficult for the square battery to dissipate heat and provide thermal runaway protection. Therefore, the positive pole of the square battery ternary battery is not suitable for developing towards ultrahigh nickel. At the same time, as mentioned above, the negative pole of the square battery is not suitable for adding too much “silicon,” so the single-cell energy density of the square battery cannot be too high.
Cylindrical batteries, on the other hand, are relatively easy to dissipate heat due to their small cell size. In addition, the application of full pole ears allows heat to be concentrated at the bottom, making it easier to dissipate heat in a targeted manner. Therefore, a more aggressive high nickel scheme can be adopted, coupled with a high silicon negative electrode, and the single-cell energy density can reach 300 Wh/kg. In the future, if a positive electrode with a nickel proportion of more than 90% is used, the single-cell energy density can reach 350-400 Wh/kg.
Overall, although the integration efficiency of square batteries is high, the single-cell energy density of 4680 cylindrical batteries is high as well. Therefore, the two have a comparable system energy density.
As a species that has been commercialized for more than 30 years, cylindrical batteries have the most mature technology and have certain advantages in terms of production efficiency, yield, and investment cost. For example, in terms of yield rate, Panasonic’s 2170 battery can achieve a yield rate of more than 99%, while a yield rate of 90% is already an excellent level for square batteries.
In addition, in terms of production efficiency, if the same winding process is used, the inherent efficiency of concentric winding of cylindrical batteries is much higher. For example, according to the latest production line of EVE Energy, 200 2170 batteries can be produced per minute, while similar production lines can only produce 10-12 square batteries within 200 Ah in one minute, and less than 10 square batteries above 200 Ah. If it is a new car with an 80-degree battery, the production of cylindrical batteries takes about 20 minutes, while square batteries take 30 minutes.If large-scale production of 4680 batteries proceeds smoothly, it is expected that after 2024, the cost per kWh of 4680 batteries will be 50-100 yuan cheaper than that of ternary square batteries. The cost of a 100 kWh electric car can be lower by 5,000-10,000 yuan.
From the perspective of the ternary battery system (including cobalt-free batteries and quaternary batteries), if the good rate of 4680 batteries can be rapidly improved, with a certain cost advantage and ultra-high charging and discharging power, they will gradually replace square ternary lithium batteries in the mid-to-high-end market.
In the mid-to-low-end market, phosphate iron lithium batteries are still dominant because they are inherently stable and not prone to thermal runaway, making them more suitable for high-efficiency integrated but poor heat dissipation square batteries. Therefore, the future situation is likely to be that some high-end models will gradually use 4680 ternary batteries, and mid-to-low-end models will mainly use CTP square phosphate iron lithium batteries.
Then CATL will face the siege of both 4680 batteries and BYD blade batteries. BYD itself started with batteries and has been focusing on phosphate iron lithium batteries for many years. With the significant expansion of the production capacity of “Freddie” batteries, as shown in the article “Accepting NIO and Xiaomi, Freddie’s offensive has just begun”, it is bound to eat up a part of CATL’s share.
However, at the just-concluded Electric Vehicle 100 People Conference 2022, CATL also launched a counterattack-CTP 3.0 version of Kirin batteries. Whether it can maintain its absolute leading position depends on the landing effect and the speed of cost reduction and efficiency enhancement of CTP 3.0.
Which automakers and battery companies are following up on the layout of large cylindrical batteries?## Current State and Future Trends of Electric Vehicle Batteries
From the perspective of the automotive industry, Tesla remains the main promoter of electric vehicle battery innovation. As of Q1 2022, Tesla has already started trial production of its 4680 battery and is expected to deliver some Model Y electric vehicles to consumers by the end of the year. The real breakthrough is expected to occur after 2023, when the long-delayed Cybertruck, Roadster 2, and heavy-duty Semi will finally hit the market. On the other hand, BMW’s 4695 battery is slated for production after 2024 and may become the main power source for the company’s future all-electric platform, “Neue Klasse.”
It is worth mentioning that there are already a number of overseas manufacturers using cylindrical batteries. For instance, Lucid and Rivian, two new electric vehicle manufacturers from the United States, currently use 2170 batteries and are expected to transition to 4680 batteries in the near future.
In terms of battery manufacturers, overseas companies dominate the industry, including Panasonic, LG Chem, Samsung SDI, and Storedot. Panasonic and LG Chem plan to start production in 2023, while Samsung SDI plans to begin production in 2024. Additionally, an Israeli company, Storedot, is also planning to commence production of 4680 batteries in 2024.
At home, CATL is planning 12GWh of 4680 battery production capability, with research and development progressing rapidly. Mass production is expected to commence in 2024, with Tesla and BMW as potential customers. By the end of 2023, EVE Energy is expected to increase its production capacity of large cylindrical batteries, and production of 4680 batteries is expected to commence in 2024. Another Chinese manufacturer, BYD, is planning to produce 4680 batteries in Europe and has set a target of 20GWh of annual production capacity.
Source: 36氪Taking a comprehensive view, compared to the upgrade from 18650 to 2170, the 4680 battery has squeezed toothpaste this time, basically determining the development direction of cylindrical batteries, and it is expected to lead the market share of cylindrical batteries to catch up with square batteries quickly. However, the 4680 battery still faces many technical challenges, such as the laser welding points of the entire pole ear battery being at least five times higher than that of 2170, and the arc-shaped edge of the entire pole ear coating requires higher precision from the equipment. In the future, the focus on the development of the 4680 battery will depend on the yield rates of companies such as Tesla, Panasonic, LG Chemical and others, stabilizing at above 90%.
Finally, welcome everyone to download the Garage App to learn about the latest new energy news. If you want to get more immediate communication, you can click here to join our community.
This article is a translation by ChatGPT of a Chinese report from 42HOW. If you have any questions about it, please email bd@42how.com.