Last Friday, Dow Chemical held two technical seminars: “Dow Organic Silicon for ADAS Encapsulation” and “Dow Chemical Solutions for New Energy Vehicles to Assist the Three Powers”. Here are some valuable excerpts for readers.
Why Choose Organic Silicon in ADAS and xEV Applications
In terms of ADAS applications, there are some underlying requirements. Specifically, our perception devices and operation platforms need to be sealed in boxes during assembly. From the material perspective, organic silicon materials have several advantages, including:
-
A wide temperature range with high stability in both high and low temperatures (-45-200 degrees): They are resistant to high temperatures and maintain elastic properties in a wide temperature range. Additionally, the typical transformation temperature of organic silicon is lower than -100℃.
-
Anti-vibration elastic modulus: Organic silicon materials maintain flexibility at high filler contents and have low modulus, which is conducive to stress relief, shock absorption, and vibration damping.
-
Good electrical insulation and resistance to water and moisture: They exhibit excellent moisture resistance and water resistance, as well as good flame retardancy.
-
Excellent flame retardancy: They show superior flame retardant performance.
-
Effective heat management: They offer high electrical conductivity and low thermal resistance.
In practical use, whether it’s perception devices such as ultrasonic radar, millimeter wave radar cameras and laser radar, or operation platforms represented by domain controllers,organic silicon materials are widely used for sealing or as thermal conductive materials.
In these three directions, the main applications include thermal conduction (thermal filling, thermal silicon grease, and thermal bonding agents), protection (sealing, dust and water protection, and potting glue), and electromagnetic shielding.
As the arms race for automotive chips begins, the design of heat dissipation for onboard chips is a major challenge, requiring the use of thermal conductive technology to quickly remove heat. For automotive power electronic devices, the materials for heat conduction between the radiator and heating elements mainly include thermal conduction pads and thermal conduction filling adhesives. Relatively speaking, thermal conduction pads are a more traditional method of heat transfer medium. Since the pads are used in a paste-like manner, a large pressure is required to overcome the gap tolerance, which puts demands on the heat generating element’s bearing capacity. After curing, thermal conduction filling adhesives possess the low stress characteristics of silica gel, which can reduce the stress generated by temperature and external pressure. The soft hardness can also resist a certain degree of vibration and impact. The use of very thin layers can achieve lower thermal resistance.
The translation result in English Markdown text is as follows, maintaining the HTML tags inside the Markdown:
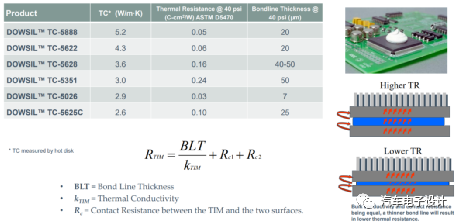
This article is a translation by ChatGPT of a Chinese report from 42HOW. If you have any questions about it, please email bd@42how.com.