Author: TruckTech Online
Introduction
Recently, Japan has completed the validation test for “platooning of driverless trucks” on open roads, and this article provides a detailed introduction to the content and related technologies used in this project.
Introduction to Japan’s Driverless Truck Platooning Project
In March 5, 2021, the Japanese Ministry of Land, Infrastructure, Transport and Tourism and the Ministry of Economy, Trade and Industry announced the successful implementation of the “platooning of driverless trucks” (also known as formation driving, convoy driving, etc.) validation test on a section of the Shin Tomei Expressway in Japan.
The road length of the test was about 15km (from the Enshumori-cho PA to the Hamamatsu SA on the Shin Tomei Expressway), with three large trucks maintaining a speed of 80km/h and a distance of 9m between them, forming a convoy. The front truck was driven by a driver, while the two rear trucks were driverless, but a safety officer was seated in the co-pilot seat of the following vehicle for safety considerations.
In order to solve the problem of the aging of truck drivers and shortage of personnel, the Japanese Ministry of Land, Infrastructure, Transport and Tourism and other government agencies had set the target of realizing the technology of driverless truck platooning on highways in 2020. The “Validation of Platoon Driving for Actual Deployment in Truck Societies” project was entrusted to Toyota Tsusho, and multiple actual verification tests on driverless truck platooning technology had been conducted until now. This activity is also part of this verification project and is still being implemented by Toyota Tsusho.
Technologies Used to Achieve Driverless Truck Platooning
Driverless truck platooning refers to multiple trucks running by following the trajectory of the front truck with the help of electronic means through communication between driver and driverless trucks.
In this event, the two most important points were to automatically track the driving trajectory of the front truck by the rear truck and to control the distance between multiple vehicles in the queue to within 10m (5m – 10m) to prevent other vehicles from easily inserting into the queue of multiple vehicles running together.The main technologies used to achieve this are “front vehicle tracking control,” “inter-vehicle distance control,” and “front driver driving assistance.”
For example, in “front vehicle tracking control,” 3D LIDAR, stereo cameras, RTK-GPS, and steering control are used to identify the trajectory of the front vehicle and control the lateral offset from the vehicle within ±50 cm.
Similarly, “inter-vehicle distance control” also uses 3D LIDAR and stereo cameras. Since existing inter-vehicle distance sensors cannot avoid collisions between trucks during emergency braking, trucks must communicate with each other to share real-time information about the use of acceleration and braking devices, ideally maintaining inter-vehicle distance. During testing, even during emergency braking at a speed of 80 km/h, the inter-vehicle distance only shortened by 2 m.
As shown in the figure, the front vehicle is manually driven, and the two following vehicles are automatically driven, with a single vehicle length of 12 m and a total queue length of about 60 m. The LED queue warning device and the external vehicle indicator have been added, and the front driver driving assistance system includes rear vehicle monitoring, rear side millimeter wave radar, and electronic rearview mirrors. The rear vehicle has lane-keeping function, and inter-vehicle distance is maintained through inter-vehicle sensors and communication.
The actual vehicle development is undertaken by the advanced mobility company. New functions added in 2019 include:
-
The front vehicle driver can operate the engine start, stop, gearbox shift, parking brake activation, and release of the following cars uniformly.
-
The front vehicle driver seat is equipped with a monitor that displays abnormal items such as engine start-up status, gear position, distance from the front vehicle, water temperature, remaining fuel, and system failure information of the following vehicles.
-
The vehicle control device is redundant, and multiple redundancies such as control ECU, steering actuator, and brake are achieved.
-
The front vehicle driver driving assistance function detects surrounding vehicles and obstacles through millimeter wave radar when changing lanes. If there are surrounding vehicles, the driver will receive a warning message on the HMI and electronic rearview mirror.
-
The LED information board installed at the rear of the truck issues a warning to the nearby vehicle that may enter the convoy, and reports the close vehicle to the front vehicle driver HMI.
-
In the event of an abnormality during convoy driving, such as a vehicle entering between convoy vehicles, the system will display an abnormal alarm on the front vehicle driver HMI, showing the location of the event and the distance from the following vehicle.- When a serious anomaly occurs that prevents queue driving, the queued vehicles enter MRM (Minimum Risk Maneuver) mode.
-
Safety technology:
-
When the device malfunctions slightly, the “degraded driving mode” is used to safely decelerate to 50 km/h;
-
When multiple malfunctions occur, the “MRM (Minimum Risk Maneuver)” mode is used;
-
If the queue following cannot be maintained, the vehicle is safely stopped.
-
In the case of inserting vehicles into the queue, when the truck queue is in a parked state, if there are pedestrians or vehicle queues, “cutting in danger” will be displayed via LED to alert others, and the driver of the leading vehicle will be unable to start.
-
During the truck queue travel, if other vehicles cut in, it will switch to MRM mode, follow the truck’s alarm lights and stop safely.
Future development direction of the project
The project has carried out road tests for over 40,000 kilometers, and many on-site driving tests, simulation tests, etc. have been carried out to achieve the originally planned high reliability and high safety goals.
In snow, dense fog and other harsh conditions where travel is impossible, these will be topics for further research in the future.
The vehicle used in this project is a box-type cargo truck, and the development of further technology is required if it is to be applied to other vehicle types, especially more demanding container tow trucks that are outside of the box-type truck.
Future development plan
The growth strategy released by the Japanese government includes “researching the operation and management system of high-performance trucks with the goal of achieving L4 level automatic driving trucks on highways after 2025.” The Ministry of Transportation will continue to promote the development and social practical application of automatic driving trucks in the future.
According to the “ITS Concept Roadmap 2020” published by the Japanese government, the goal is to commercialize rear car unattended queue following of high-speed highway trucks after the 2022 fiscal year.
In the future, technology development will be promoted to meet the requirements of various driving environments such as rain, snow, and night driving.
Currently, new projects that may be implemented from 2021 onwards are being discussed, with the goal of achieving a queue of trucks equipped with L4 level automatic driving technology, such as switching to automatic driving mode and continuing to travel after the queue is forced to cancel.
Future commercialization plan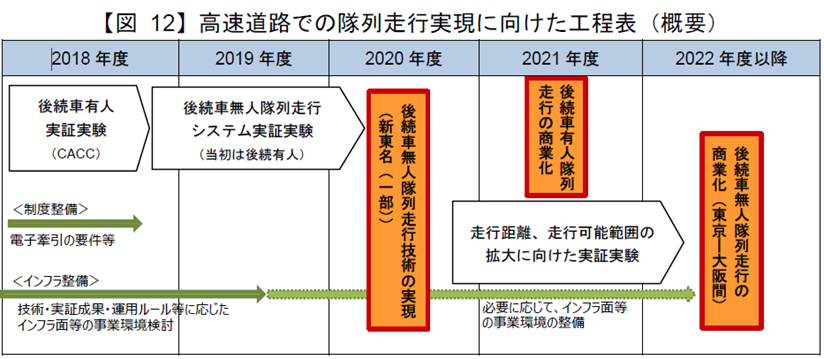
Regarding the commercialization timeline, officials from the Ministry of Industry and Information Technology stated that “the goal is to achieve commercialization of platooning with human operation in 2021. The original plan of the Growth Strategy released in 2019 was to achieve commercialization of platooning with autonomous driving after 2022. However, it was found in the practical process that it is difficult to completely solve some situations with only platooning technology of unmanned operation. It may be necessary to combine with L4 level autonomous driving technology to strive for commercialization. Therefore, a new project targeting L4 level autonomous driving is planned to be launched, and the commercialization of L4 level trucks is expected to be achieved after 2025. It is hoped that platooning technology can be included in the L4 level technology.”
Regarding the specific form of commercialization, there is no conclusive conclusion yet. There may be multiple forms, and truck manufacturers may sell the technology by configuring it into truck products or advanced mobility companies and other third parties may sell the modified vehicles. In short, the goal is to facilitate the application of the logistics industry.
This article is a translation by ChatGPT of a Chinese report from 42HOW. If you have any questions about it, please email bd@42how.com.